HIGH TWIST GUT STRINGS
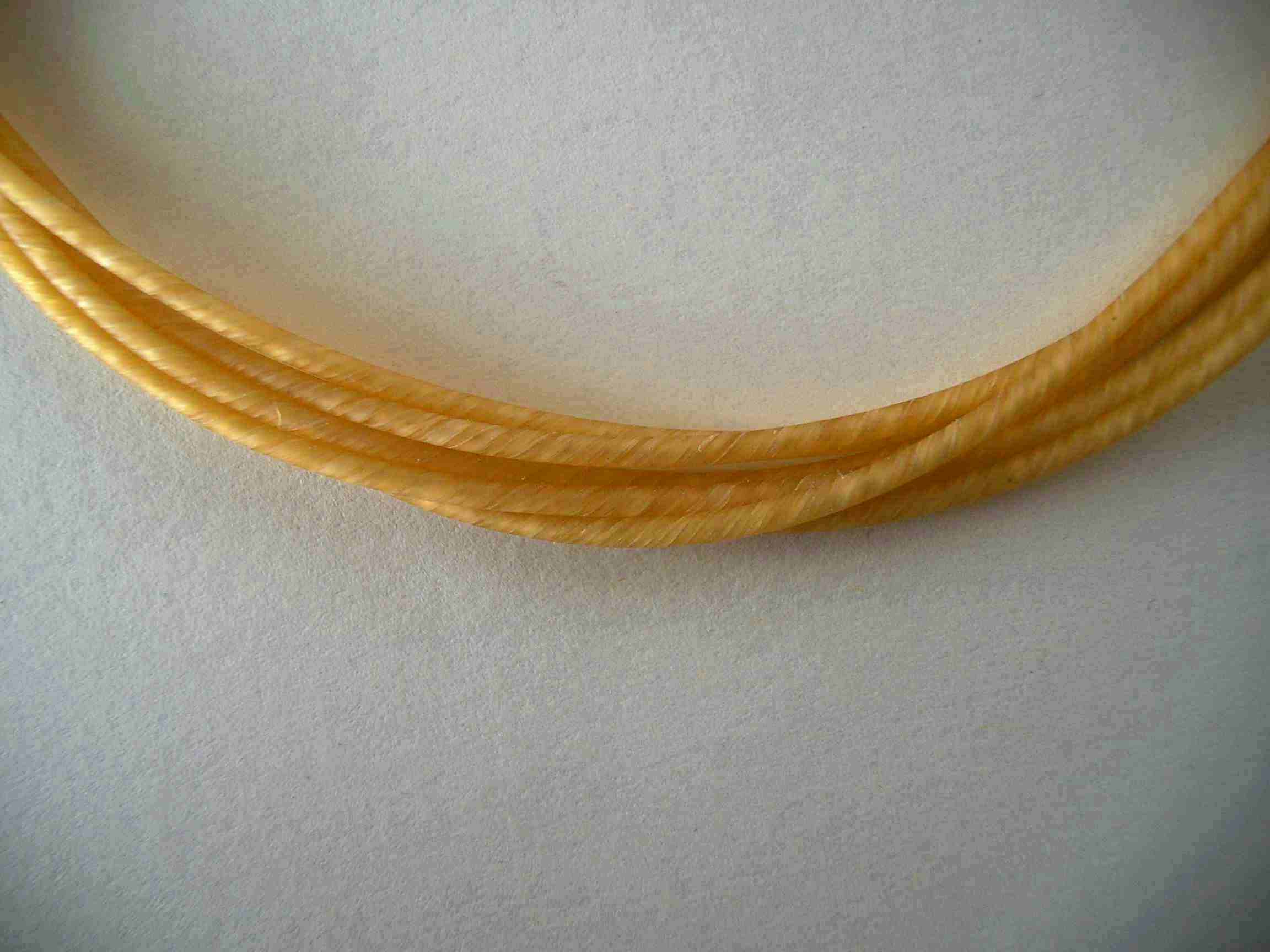
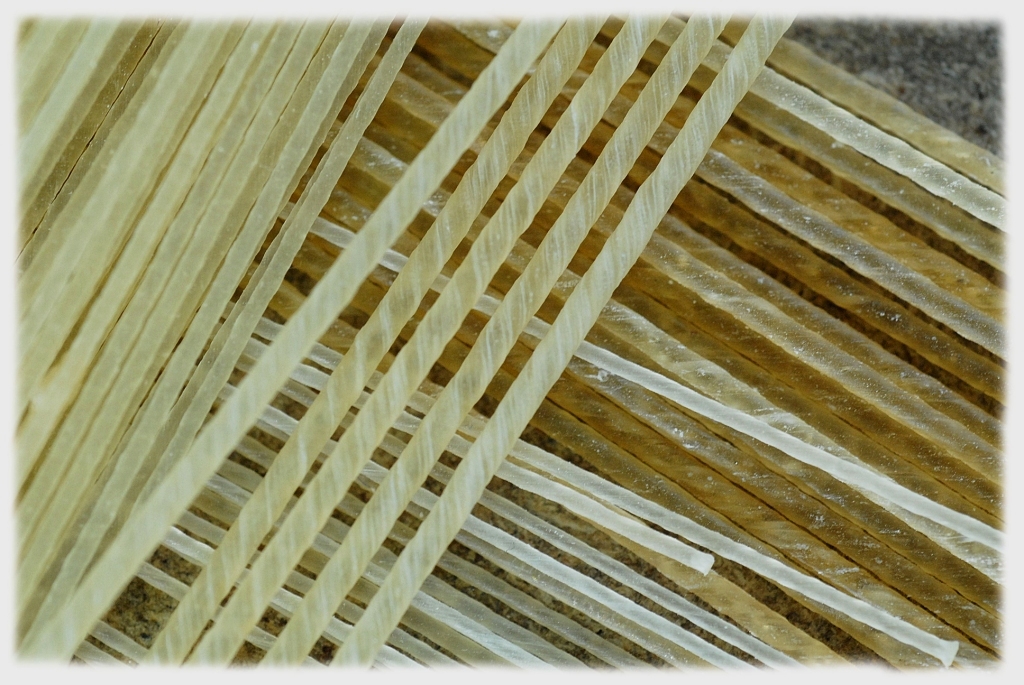
INTRODUCTION
The origin of the employment of gut to make musical strings is lost in the mists of time. Along the centuries manufacturing techniques were gradually refined until they reached the perfection unanimously recognized as the trademark of Italian and French stringmakers in the 17th to 19th century.
The scope of our work, supported by constant research and painstaking experimentation, is to offer natural gut strings produced by modern craftsmen working in the ancient Italian/French string-makers manufacturing criteria that for centuries has been passed on from one generation to the next, sure to offer you the very best of our tradition and aiming to reach the magic of sound that only gut, of all materials, can achieve.
TECHNICAL SPECIFICATIONS AND FIELD OF APPLICATION
First choice plain gut strings for general use in high and mid registers. All strings more than 0.50 mm. in diameter are exclusively high twist and undergo a specific processing aiming to ensure maximum elasticity and grant the best acoustical performance, ease of attack and long playing life, as proven by many acoustics and wear-and-tear tests.
The new product we offer instead of the varnished gut strings are the semi-rectified strings (we call them half-rectified).
String -varnishing is a modern treatment which was never used historically (gut strings were kept in olive or almond oil) and its sole purpose is granting a longer string playing life. But this happens at the cost of other aspects, the most important being a loss of sound quality, brightness for example, but also the bowing attack is not as efficient as with unvarnished gut.
The surface of the half- rectified strings is only partly rectified, imitating the manual polishing techique of the time just to obtain a true string.
With this method the amount of fibers damaged by the abrasive action is noticeably reduced as compared with strings rectified with modern procedures. The advantages are: better stability against climatic changes, longer playing life and better acoustic performance.
We tested these strings for a long time: they best imitate historic hand- polishing in that they damage only a small amount of gut fibers as compared with current rectifying methods.
The advantages are:
an improved stability by climatic changes, longer playing life (similar to those of the vernished ones) and superior acoustical performance.
Owing to the special manufacturing technique employed in the production of the half-rectified string type, the diameters in this table indicate a mean value.
E.g. a 66 string indicates, in fact, a possible diameter-window between 65 and 67.
Please notice
Gut is liable to suffer from cutting edges. Before stringing the instrument do make sure the nut and bridge are free from sharp edges and the nut grooves not too deep and perfectly smooth.
You can get rid of sharp edges with very fine grit sandpaper (600, for example) or the finest steelwool (000).
The best sound quality develops when the strings have completely set, which may ordinarily take sometime. To achieve a stable intonation in just a few minutes you can repeatedly pinch each string at midlength with your fingers, pull it decidedly sideways and tune it up again. Stop when the string does not pull out of tune anymore.
NOT ALL GUT STRINGS ARE ALIKE: THE DIFFERENCE IS MADE BY THE RESPECT TO THE MANUFACTURING PROCESSES FOLLOWED FOR CENTURIES BY THE STRINGMAKING MASTERS.
Note: gauges are expressed in hundred of millimeters (i.e. 120 = 1,20 mm).
DOUBLE TWIST GUT STRINGS "V" TYPE
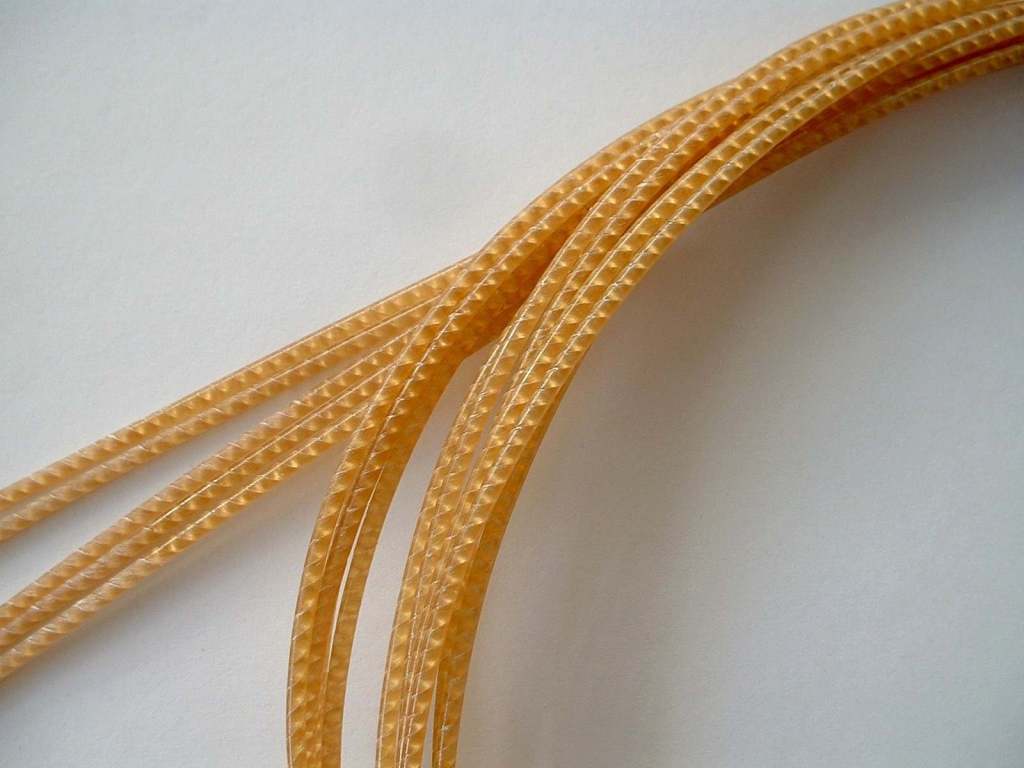
INTRODUCTION
In the 16th and 17th century in iconographical sources the strings on musical instruments are depicted as smooth, rather curly and, in the tract coming out of the peg box, they are often bundled up like they were made of soft cord. This suggests that at time the strings were extremely pliable, which would obviously affect their acoustical performance. On the contrary, modern gut strings, because of their stiffness, can only be made up in circular coils, lest they get damaged. Starting from this important observation and supported by other historical information we created our " VENICE " strings.
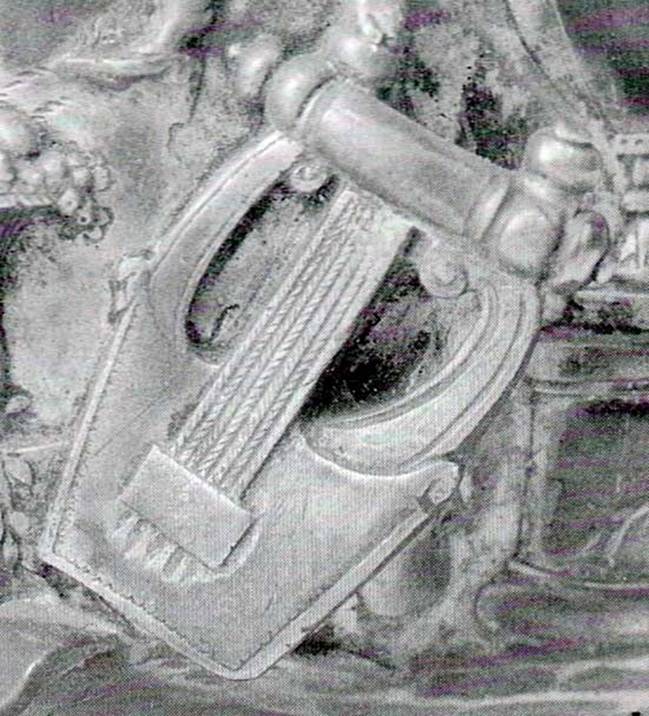
Silver cup of the empire roman- age: Cithara string detail (from the Berthouville treasure, Normandy)
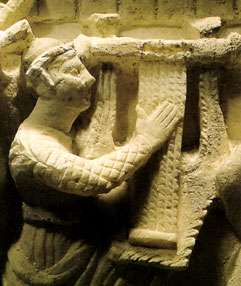
Etruscan urn of the II – I centrury a.C.: Cithara string detail (Museo Etrusco “Guarnacci” of Volterra, Italy)
TECHNICAL SPECIFICATIONS AND FIELD OF APPLICATION
The Venice strings possess a remarkable degree of elasticity and pliability, superior to any strings currently on the market. This means a surprisingly ready attack and good richness in upper overtones.
Available in a wide choice of diameters and lengths, the VENICE strings are particularly suited for the mid registers of Renaissance and Baroque stringing, e.g. as 2nd and 3rd Violin, 3rd and 4th renaissance- Gambas (Tenor and Bass expecially); Lute mid registers, 2nd and 3rd Violone etc.
The new product we offer instead of the polished Venice gut strings are the semi-rectified ones (we call them half-rectified).
The surface of the half- rectified strings is only partly rectified, imitating the manual polishing techique of the time just to obtain a true string.
With this method the amount of fibers damaged by the abrasive action is noticeably reduced as compared with strings rectified with modern procedures. The advantages are: better stability against climatic changes, longer playing life and better acoustic performance.
We tested these strings for a long time: they best imitate historic hand- polishing in that they damage only a small amount of gut fibers as compared with current rectifying methods.
Owing to the special manufacturing technique employed in the production of the half-rectified string type, the diameters in this table indicate a mean value.
E.g. a 120V string indicates, in fact, a possible diameter-window between 118 and 122.
Note: gauges are expressed in hundred of millimeters (i.e. 120 V = 1,20 mm).
RECTIFIED NYLGUT® STRINGS "NG" TYPE
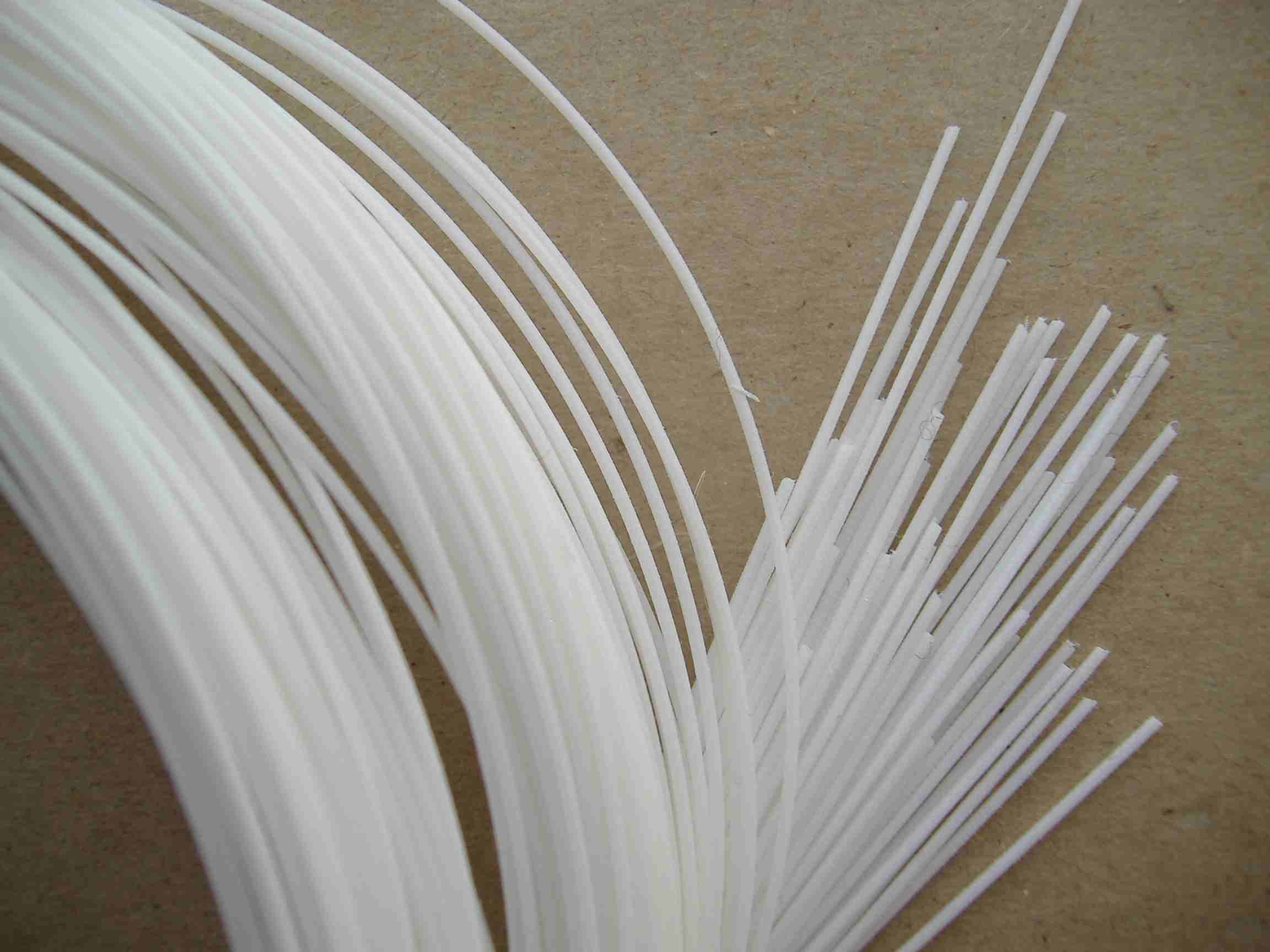
INTRODUCTION
The development of a new synthetic material that can imitate the acoustical characteristics of gut but without the typical defects such as high cost, short string life, and severe instability to changes of climate, has always been a fundamental goal of our research. Nylgut® * represents the fruit of this research and is a perfect synthesis of the acoustical properties of nylon and of PVF (carbon) strings.
TECHNICAL CHARACTERISTICS AND FIELD OF APPLICATION
Nylgut®, distinguishable by its milk-white color, has the same gut's density (gauges are the same of the gut) and acoustical qualities similar to that material. It should be considered the first "synthetic" version of the natural product.
Other strong points of Nylgut® are its' elevated resistance under tension -greater than that of gut- but even more important is its extraordinary immunity to changes of climate, considerable superior to that of nylon and gut, thereby guarantying an insuperable stability of tuning under normal conditions.
Nylgut® can be used advantageously for the substitution of nylon and gut strings for plucked string instruments such as lutes, guitars and harps (modern harps included). For example, Nylgut® strings are particularly well suited for the 1st through 5th courses of the renaissance and d minor-baroque lutes, FRETS INCLUDED.
Special length (200 cm): see the NGE type.
Please notice
Just like gut, Nylgut® is liable to suffer from cutting edges. Before stringing the instrument do make sure the nut and bridge are free from sharp edges and the nut grooves not too deep and perfectly smooth.
You can get rid of sharp edges with very fine grit sandpaper (600, for example) or the finest steelwool (000).
The best sound quality develops when the strings have completely set, which may ordinarily take sometime. To achieve a stable intonation in just a few minutes you can repeatedly pinch each string at midlength with your fingers, pull it decidedly sideways and tune it up again. Stop when the string does not pull out of tune anymore.
Note: gauges are expressed in hundred of millimeters (i.e. 120 = 1,20 mm).
NYLGUT® WOUND STRINGS - "D" TYPE
First quality wound strings with vernished copper wire, manufactured according to our best experience. The innovative idea was to employ a Nylgut® multifilament core -very stable to the moisture changing- and to partly limit the production of the very high overtones giving the metallic edge that is generally present in the strings of this type and never welcome by early music lovers. The thinner strings, the ones more subject to wear-and-tear, are protected by a light superficial vernish which also grants a longer playing life.
Diameters are expressed in equivalent solid gut (i.e. a 73D = .73 mm gut string)
THE EQUIVALENT SOLID GUT
To keep calculations simple and make it possible to use any available string-calculator, C type loaded gut strings, as well as wound Nylgut ones D and DE types, are referred to by a letter following a number indicating the equivalent diameter of a plain gut string.
E. g. "140 C" or "140D"stands for strings (indicated by the letter "C" or "D") corresponding to a plain gut string 1.40 mm. in diameter. The actual diameter of the strings is, of course, smaller but under playing conditions it will have the same working tension as a plain gut string of 140 mm. diameter at equal pitch.
ALCHEMIA (New Nylgut®) STRINGS TYPE
Until the mid-20th century all Treble guitar strings were made in gut, a material that had been used for thousand of years and that combines good promptness of attack and excellent performances . A fundamental aim of our research has therefore been to design a new synthetic product having the same acoustic properties as gut without its typical defects (high cost, short lifetime, high instability under moisture changes). Our New Nylgut® has precisely all these good qualities without all these defects.
Its features include promptness of attack, excellent performances and a truly remarkable stability of intonation under moisture changes. The Alchemia Basses are wound with of genuine pure silver that ensures the highest possible response in terms of performances, lower interference from finger noise and long lifetime. The wound strings have also been designed according to the principle - absolutely new - of progressively increasing the dynamic performance of the bass register to compensate for the human ear's natural tendency to perceive lower frequencies less audibly.
SETS FOR BAROQUE BOWED INSTRUMENTS
(calculated for a'-415 Hz.)
BAROQUE VIOLIN (stringing type after 1690 ca.)
Gut string length: 120 cm.
These sets were conceived bearing in mind the current string diameters strandards and scaling tension profile
|
|
Light |
Medium |
Heavy |
e |
high twist gut |
62 |
64 |
66 |
a |
high twist gut |
79 |
82 |
85 |
a |
Venice "V" type |
82 V |
85 V |
88 V |
d |
high twist gut |
104 |
108 |
112 |
d |
Venice "V" type |
108 V |
112 V |
116 V |
G |
silver wound "F" type |
Light (155 equiv gut) |
Medium (160 equiv gut) |
Heavy (165 equiv gut) |
BAROQUE VIOLIN (stringing type before 1690 ca.)
Gut string length: 120 cm.
These sets were conceived bearing in mind the current string diameters strandards and equal feeling profile
|
|
Light |
Medium |
Heavy |
e |
high twist gut |
62 |
64 |
66 |
a |
high twist gut |
88 |
91 |
94 |
a |
Venice "V" type |
91 V |
94 V |
97 V |
d |
high twist gut |
124 |
128 |
132 |
d |
Venice "V" type |
128 V |
132 V |
136 V |
d |
loaded gut "C" type |
128 C |
132 C |
136 C |
G |
Venice "V" type |
170 V |
180V |
190 V |
G |
loaded gut "C" type |
170 C |
180 C |
190 C |
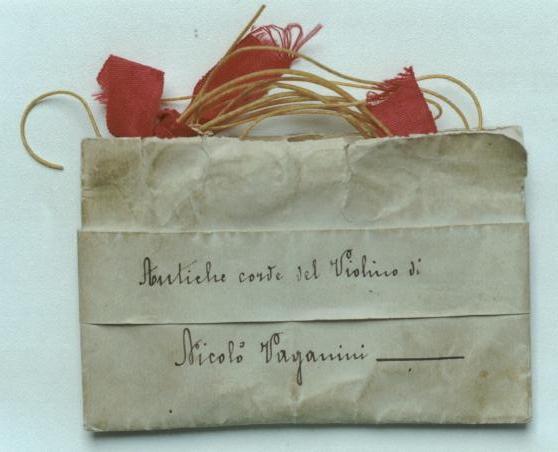
Genoa 2002: Paganini strings
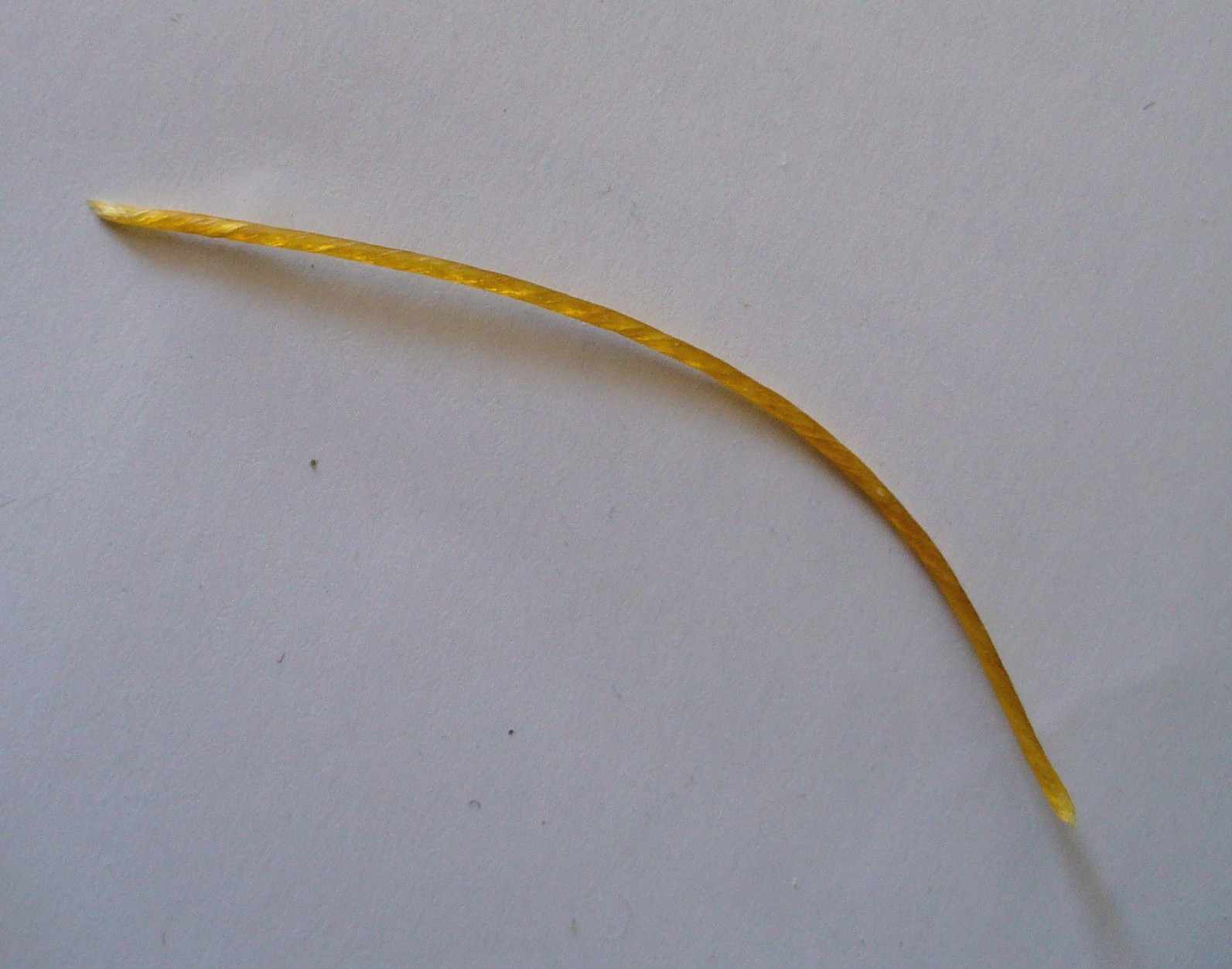
Genoa 2002: Paganini's E string .71 mm gauge
Violin historical string sets (gauges developed according to historical sources)
The diameters suggested here were the rule for violin strings from the mid-18th to the end of the 19th century, as indicated by the substatial documentation of the time.
Especially the medium tension diameters correspond to those of the strings that belonged to Paganini, (ca. 1840) which we measured in April 2000 and other sources.
We strongly suggest here the use of the half rectified gut strings: the surface of these strings is only partly rectified, imitating the manual polishing techique of the time. With this method the amount of fibers damaged by the abrasive action is noticeably reduced as compared with strings rectified with modern procedures. The advantages are: better stability against climatic changes, longer playing life and better acoustic performance.
The 4th string is made according to F. Galeazzi (Rome 1792) and Louis Spohr (1832).
|
TYPE |
Light |
Medium |
Heavy |
e |
high twist gut |
66 |
70 |
73 |
a |
high twist gut |
85 |
88 |
91 |
d |
high twist gut |
112 |
116 |
124 |
G |
pure silver wound "F" type |
Light (170 equiv gut) |
Medium (175 equiv gut) |
Heavy (180 equiv gut) |
BAROQUE VIOLA
Gut string length: 120 cm.
These sets were conceived bearing in mind the current string diameters strandards
TYPE | Light | Medium | Heavy | |
a | high twist gut | 79 | 82 | 85 |
d | high twist gut | 104 | 108 | 112 |
g | silver wound "F" type | Light (160 equiv gut) |
Medium (165 equiv gut) | Heavy (170 equiv gut) |
C | silver wound "F" type | Light (220 equiv gut) | Medium (230 equiv gut) | Heavy (240 equiv gut) |
Viola historical string sets (gauges developed according to historical sources)
Suggested diameters represent a mean value as inferred from historic sources from the 18th and 19th centuries. From those sources it is possible to ascertain that the viol was strung with the same strings as the violin, minus the E treble and plus an overspun bottom C.
We strongly suggest here the use of the half rectified gut strings: the surface of these strings is only partly rectified, imitating the manual polishing techique of the time. With this method the amount of fibers damaged by the abrasive action is noticeably reduced as compared with strings rectified with modern procedures. The advantages are: better stability against climatic changes, longer playing life and better acoustic performance.
The 3rd and 4th strings are made according to F. Galeazzi (Rome 1792).
TIPO | Light | Medium | Heavy | |
a | high twist gut | 85 | 88 | 91 |
d | high twist gut | 112 | 116 | 124 |
g | silver wound "F" type | Light (170 equiv gut) |
Medium (175 equiv gut) | Heavy (180 equiv gut) |
C | silver wound "F" type | Light (260 equiv gut) | Medium (270 equiv gut) | Heavy (275 equiv gut) |
BAROQUE CELLO
Gut string length: 120 cm.
These sets were conceived bearing in mind the current string diameters strandards
TYPE | Light | Medium | Heavy | |
a | high twist gut | 112 | 116 | 120 |
d | high twist gut | 150 | 155 | 160 |
G | high twist gut* | 200 | 210 | 220 |
G | silver wound "F" type | Light (240 equiv gut) | Medium (250 equiv gut) | Heavy (260 equiv gut) |
C | silver wound "F" type | Light (360 equiv gut) | Medium (380 equiv gut) | Heavy (390 equiv gut) |
* for repertoires before 1720 ca. only
Cello historical string sets (gauges developed according to historical sources)
Suggested diameters represent a mean value as inferred from historic sources from the 17th and 18th centuries.
We strongly suggest here the use of the half rectified gut strings: the surface of these strings is only partly rectified, imitating the manual polishing techique of the time.
With this method the amount of fibers damaged by the abrasive action is noticeably reduced as compared with strings rectified with modern procedures. The advantages are: better stability against climatic changes, longer playing life and better acoustic performance.
The overspun 3rd and 4th strings are made according to common17th and 18th centuries string making criteria.
TYPE | Light | Medium | Heavy | |
a | high twist gut | 120 | 124 | 132 |
d | high twist gut | 165 | 170 | 180 |
G | silver wound "F" type | Light (245 equiv gut) |
Medium (255 equiv gut) | Heavy (275 equiv gut) |
C | silver wound "F" type | Light (365 equiv gut) | Medium (375 equiv gut) | Heavy (410 equiv gut) |
VIOLONCELLO DA SPALLA
Gut string length: 120 cm.
TYPE | Medium | Heavy | |
e | high twist gut | 100 | 104 |
a | high twist gut | 128 | 136 |
d | Double silver wound "F" type | Medium (190 equiv gut) |
Heavy (205 equiv gut) |
G | Double silver wound "F" type | Medium (280 equiv gut) | Heavy (305 equiv gut) |
C | Double silver wound "F" type | Medium (430 equiv gut) | Heavy (455 equiv gut) |
- VIOLA D'AMORE -
Gut string length: 120 cm.
TYPE | Medium | Heavy | |
d'' | high twist gut | 60 | 64 |
a' | high twist gut | 76 | 79 |
f#' | high twist gut | 91 | 97 |
d | high twist gut | 108 | 112 |
a | silver wound "F" type | Medium (145 equiv gut) |
Heavy (150 equiv gut) |
D | silver wound "F" type | Medium (210 equiv gut) | Heavy (220 equiv gut) |
A | silver wound "F" type | Medium (280 equiv gut) | Heavy (295 equiv gut) |
- DOUBLEBASS -
Gut string length: 180 cm.
TYPE | Light | Medium | Heavy | |
G | high twist gut | 220 | 230 | 240 |
D | high twist gut | 300 | 310 | 320 |
D | Venice "V" type |
300 V | 320 V | 340 V |
AA | high twist gut | 400 | 420 | 440 |
AA | Venice "V" type | 400 V | 440 V | 460 V |
AA | silver wound "F" type | Light (400 equiv gut) |
Medium (420 equiv gut) | Heavy (460 equiv gut) |
EE | silver wound "F" type | Light (540 equiv gut) |
Medium (580 equiv gut) | Heavy (620 equiv gut) |
DD/ CC |
silver wound "F" type | Light (680 equiv gut) | Medium (730 equiv gut) | Heavy (780 equiv gut) |
- DOUBLEBASS (Viennese tuning) -
Gut string length: 180 cm.
TYPE | Light | Medium | |
A | high twist gut | 200 | 210 |
E | high twist gut | 260 | 280 |
E | Venice "V" type |
280 V | 320 V |
H | silver wound "F" type | Light (345 equiv gut) | Medium (370 equiv gut) |
FF# | silver wound "F" type | Light (460 equiv gut) | Medium (495 equiv gut) |
- PARDESSUS -
Gut string length: 120 cm.
TYPE | Medium | Heavy | |
g | low twist gut | 42 | 44 |
d | low twist gut | 54 | 56 |
a | high twist gut | 70 | 73 |
f | high twist gut | 85 | 88 |
c | high twist gut | 116 | 120 |
G | silver wound "F" type | Medium (160 equiv gut) | Heavy (165 equiv gut) |
- TREBLE -
Gut string length: 120 cm.
TYPE | Medium | Heavy | |
d | high twist gut | 56 | 60 |
a | high twist gut | 73 | 76 |
e | high twist gut | 94 | 100 |
e | Venice "V" type |
100 V |
104 V |
c | high twist gut | 116 | 124 |
c | Venice "V" type | 120 V |
128 V |
c | loaded gut "C" type |
116 C |
124 C |
G | loaded gut "C" type | 150 C |
160 C |
G | silver wound "F" type | Medium (150 equiv gut) | Heavy (160 equiv gut) |
D | loaded gut "C" type | 240 C | 255 C |
D | silver wound "F" type | Medium (240 equiv gut) | Heavy (240 equiv gut) |
- TENOR -
Gut string length: 120 cm.
TYPE | Medium | Heavy | |
g | high twist gut | 60 | 64 |
d | high twist gut | 76 | 82 |
a | high twist gut | 100 | 108 |
a | Venice "V" type |
104 V |
112 V |
f | high twist gut | 128 | 136 |
f | Venice "V" type | 132 V |
140 V |
C | loaded gut "C" type |
170 C |
180 C |
C | Venice "V" type | 180 V |
190 V |
C | silver wound "F" type | Medium (170 equiv gut) | Heavy (180 equiv gut) |
G | loaded gut "C" type | 240 C | 260 C |
G | Venice "V" type | 260 V | 280 V |
G | silver wound "F" type | Medium (240 equiv gut) | Heavy (260 equiv gut) |
- RENAISSANCE BASS VIOL -
Gut string length: 120 cm.
TYPE | Medium | Heavy | |
d | high twist gut | 73 | 76 |
a | high twist gut | 91 | 94 |
e | high twist gut | 120 | 124 |
e | Venice "V" type |
124 V |
128 V |
c | high twist gut | 150 | 155 |
c | Venice "V" type | 155 V |
160 V |
G | loaded gut "C" type |
210 C |
220 C |
G | Venice "V" type | 220 V |
240 V |
G | silver wound "F" type | Medium (210 equiv gut) | Heavy (220 equiv gut) |
D | loaded gut "C" type | 270 C | 280 C |
D | Venice "V" type | 280 V | 320 V |
D | silver wound "F" type | Medium (270 equiv gut) | Heavy (280 equiv gut) |
- BAROQUE BASS VIOL (6 or 7 strings) -
Gut string length: 120 cm.
TYPE | Medium | Heavy | |
d | high twist gut | 73 | 76 |
a | high twist gut | 91 | 94 |
e | high twist gut | 120 | 124 |
c | high twist gut | 150 |
155 |
G | silver wound "F" type |
Medium (200 equiv gut) | Heavy(210 equiv gut) |
D | silver wound "F" type | Medium (270 equiv gut) | Heavy(280 equiv gut) |
A | silver wound "F" type | Medium (360 equiv gut) | Heavy(370 equiv gut) |
- VIOLONE in D -
Gut string length: 180 cm.
(v.l. = 95 cm)
TYPE | Medium | Heavy | |
d | high twist gut | 140 | 145 |
A | high twist gut | 170 | 180 |
A | Venice "V" type |
180 V |
190 V |
E | high twist gut | 230 |
240 |
E | Venice "V" type | 240 V |
260 V |
C | silver wound "F" type |
Medium (300 equiv gut) | Heavy (320 equiv gut) |
GG | silver wound "F" type | Medium (420 equiv gut) | Heavy (440 equiv gut) |
DD | silver wound "F" type | Medium (540 equiv gut) | Heavy (580 equiv gut) |
- VIOLONE in G -
Gut string length: 180 cm.
(v.l. = 85 cm)
TYPE | Medium | Heavy | |
g | high twist gut | 104 | 108 |
d | high twist gut | 132 | 140 |
d | Venice "V" type |
136 V |
145 V |
A | high twist gut | 170 |
190 |
A | Venice "V" type | 180 V |
200 V |
F | high twist gut | 220 | 240 |
F | Venice "V" type | 240 V |
260 V |
C | silver wound "F" type | Medium (320 equiv gut) | Heavy (330 equiv gut) |
GG | silver wound "F" type | Medium (420 equiv gut) | Heavy (430 equiv gut) |
The Francesco Galeazzi's 1st recipe (Rome 1791)
Field of application
For those convinced that authentic criteria should be adopted where possible, we propose a rosin that scrupulously follows the indications of an Italian-recipe dating to the mid 18th century.
It guarantees excellent quality even in prohibitive climatic conditions and its characteristics are such that it can be used on any string instrument.
Equal tension, equal feel and scaling tension
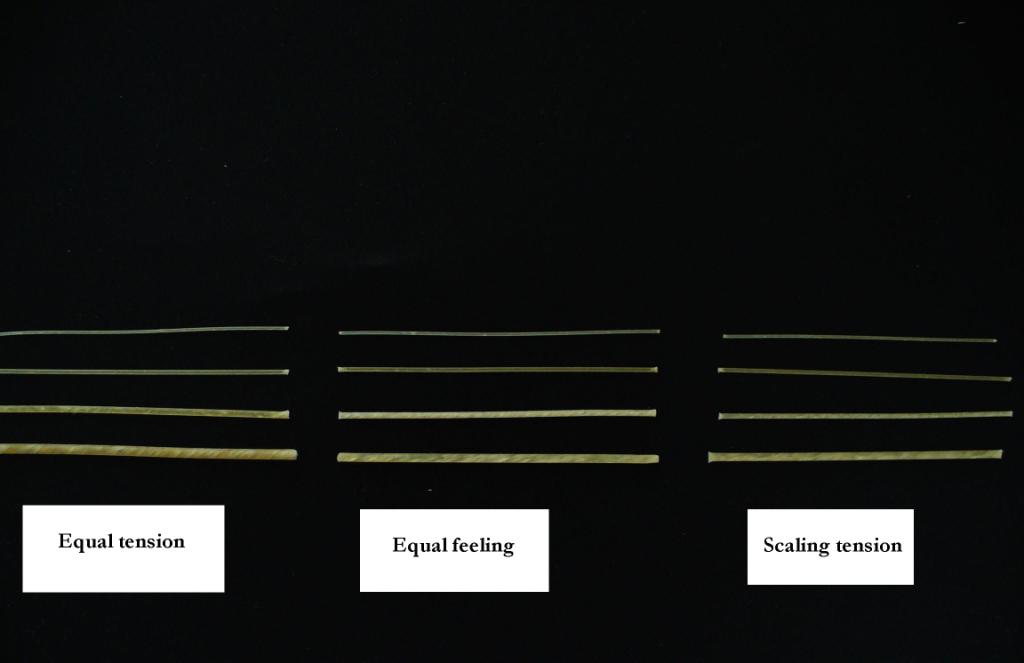
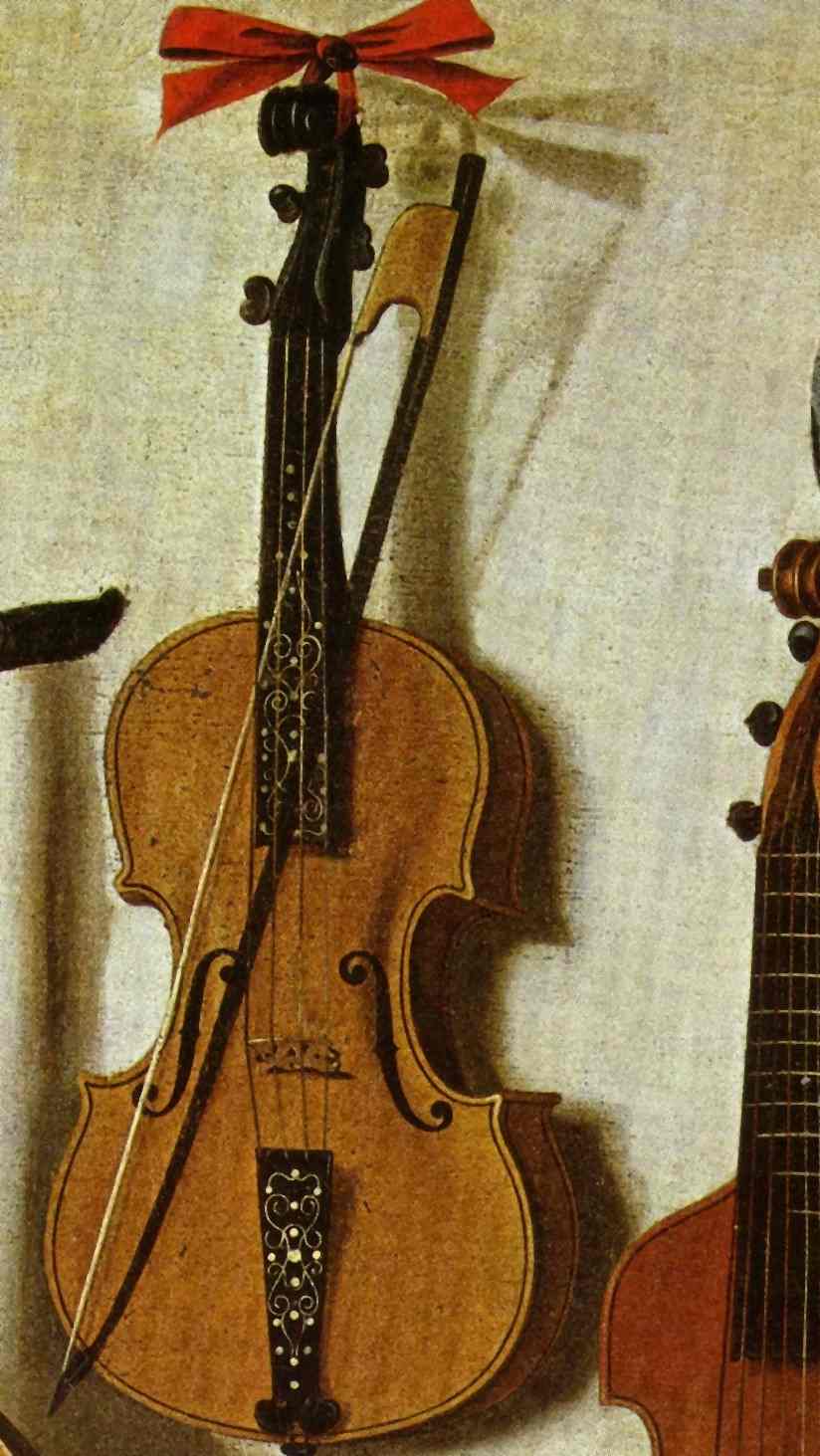
Anonymous 17th C. dutch painter; detail of a Violin. Equal tension, equal feling or scaling tension?
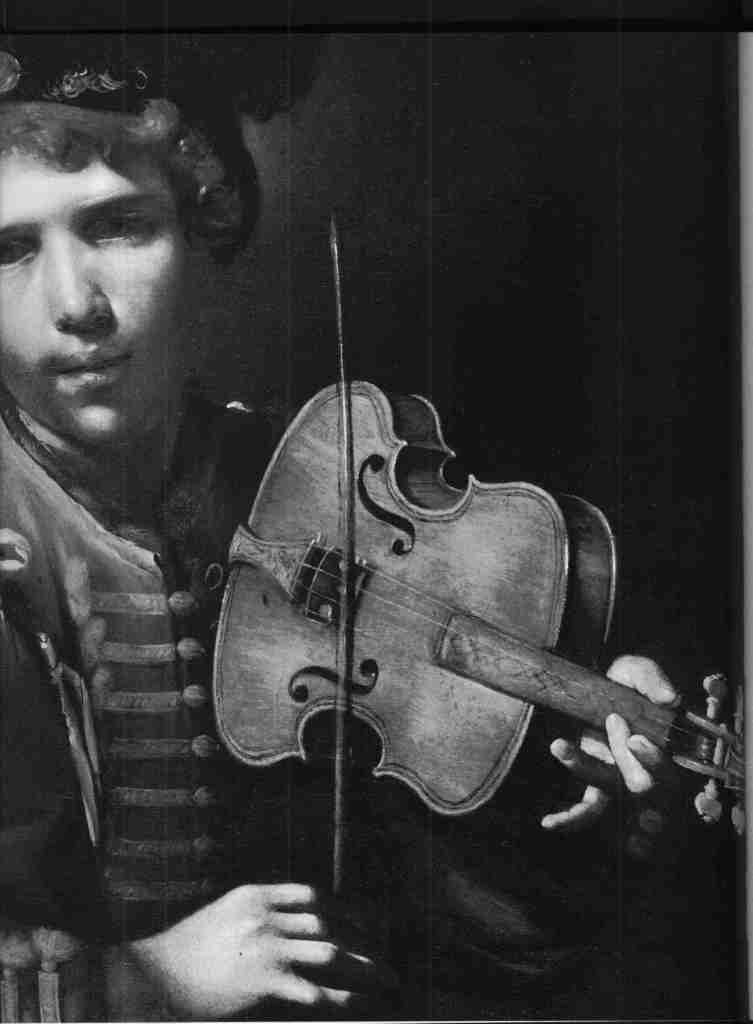
17th C. paint: detail of a Viola. Equal tension, equal feling or scaling tension?
The 17th, and expecially 18th and 19th century violin-stringings do not at all lead to stringings with a system of equal tension but instead to one of the equal feeling for the 17th C. and scaled type for the following two centuries (for comparison, an arrangement in equal tension, starting for example from a chanterelle E of 0.70 mm, would give the following diameters: E = 0.70 mm, A = 1.05 mm, D = 1.60 mm).
Today it is commonly held that a correct stringing for the violin (or for another bowed/plucked-instrument) must have all the strings at the same tension (in other words, with the same kg), but in fact this is not at all how things stand.
Before pursuing the analysis of the documentation we must therefore tackle this fundamental point, for it affects the way we reconstruct the stringings of all the plucked and bowed instruments of the Renaissance and Baroque ages expecially – not only the violin.
Let us begin our discussion of this subject with the concept of ‘tactile sensation of stiffness’. For it needs to be stressed that when a musician applying the pressure of his fingers evaluates the tension of the strings of his instrument, he is actually not evaluating the kg of tension at all, but instead the sensation of tension, which is quite another matter.
It comes natural to ask what criteria were used to evaluate a stringing in the past. This, for example, is what certain seventeenth-century treatises write about the lute (anyway, the same considerations must be applied with the bowed instruments):
"Of setting the right sizes of strings upon the lute. [...] But to our purpose: these double bases likewise must neither be stretched too hard, nor too weake, but that they may according to your feeling in striking with your thombe and finger equally counterpoyse the trebles" (John Dowland in 'Varietie of Lute Lessons', 1610).
“When you stroke all the stringes with your thumbe you must feel an even stiffnes which proceeds from the size of the stringes" (The Mary Burwell Lute Tutor, 1670 ca).
"The very principal observation in the stringing of a lute. Another general observation must be this, which indeed is the chiefest; viz. that what siz'd lute soever, you are to string, you must so suit your strings, as (in the tuning you intend to set it at) the strings may all stand, at a proportionable, and even stiffness, otherwise there will arise two great inconveniences; the one to the performer, the other to the auditor. And here note, that when we say, a lute is not equally strung, it is, when some strings are stiff, and some slack" (Thomas Mace in Musik's Monument 1676).
From the treatises of the XVII century one deduces therefore that the criterion for choosing the right string 'tension' in a given stringing responded above all to principles of empiricism: the strings were expected to be neither too tense nor too slack but to have a just degree of tension; and what is important, this tension was expected to be evenly distributed among all the strings. It goes without saying that any judgement of the degree of tension is merely subjective. A different matter, on the other hand, is the search for evenness of tension between the strings, which is the true, shared criterion of reference.
In conclusion, when the early documents use the words equal tension (and we find them until at least the end of the eighteenth century) they consistently mean equal feel and not equal kg, as instead is commonly done today.
A pertinent example is the following passage from Galeazzi (1791 year): "la tensione dev'esser per tutte quattro le corde la stessa, perchè se l’una fosse più dell'altra tesa, ciò produrrebbe sotto le dita, e sotto 1'arco una notabile diseguaglianza, che molto pregiudicherebbe all'eguaglianza della voce" (the tension must be the same for all four strings, because if one were more tense than another, that would create under the fingers, and under the bow, a considerable inequality very prejudicial to the equality of tone).
Here tension clearly means feel; as is equally plain in Bartoli's treatise: "Quanto una corda è piu vicina al principio della sua tensione, tanto ivi e piu tesa. [...] Consideriamo hora una qualunque corda d' un liuto: ella ha due principj di tensione ugualissimi nella potenza, e sono i bischieri dall’un capo, e '1 ponticello dal1'altro; adunque per lo sopradetto, ella è tanto piu tesa, quanto piu lor s'avvicina: e per conseguente, e men tesa nel mezzo" (The closer a string is to the beginning of its tension, the tenser it is. [...] Just consider any lute string. It has two beginnings of tension that are absolutely equal in power: the pegs at one end, the bridge at the other. As a result, it will be tenser the nearer it is to those points and less tense in the middle) (17th c).
To try and give some kind of scientific expression to the concepts of ‘even stiffness’, ‘equally strung’, etc. described in the treatises is in itself a somewhat complex matter, both because there is no conclusive proof that by ‘feel’ they all meant the same thing and also because that ‘feel’ can be also understood in a, so to speak, broader sense.
A preliminary distinction (when evalutuating the degree of ‘tension’) can be made, for example, by deciding whether in pressing down on the strings it is directly the fingers or the bow hairs, for in the latter case the thicker strings can oppose more resistance to the rubbing movement, thereby giving the musician the sensation of a certain unevenness. To resolve this specific problem the use of scaled tension was justified on the violin by Plessiard (mid XIX C.).
In the likely hypothesis that it is the fingers (and not the bow) that are required to assess the tension of the strings, we can again understand ‘feel’ in at least two ways. The first (that commonly accepted, by the present writer as well) considers the effort required to impart a certain meaure of lateral displacement to a string, which obviously opposes the pressure exerted. If we replace the finger with a weight acting at the same point, we can exactly measure the quantity of lateral displacement for every string examined. The second hypothesis considers that a thinner string, which digs more deeply into the finger tip pressing down on it, would produce a greater sensation of tension than a thicker string, which, having a wider surface, does not ‘dig into’ the finger to the same extent. According to this second interpretation, therefore, ‘equal feel’ involves more tension in kg in the thicker strings than in the thinner. However, we have never yet had practical evidence that the bass strings have more tension than the higher ones.
Let us therefore examine the first hypothesis better: in other words, that which considers ‘feel’ to be the sensation of resistance given by a string pressed by the fingers and ‘equal feel’ to mean that this sensation is the same also for tuned strings of different diameters; in other words, that when the same weight acts at the same point, the lateral displacement encountered is the same. The vibrating length obviously has to remain constant.
According to the laws of physics such a conception of equal feel corresponds exactly to a stringing of equal tension.
That is true, however, on condition that the initial diameters of the strings (as measured with the strings not yet mounted) remain unvaried even after they have been tuned, i.e. under tension. In pratice, however, and especially with gut, this never happens: once the strings have been tuned to the required note, their respective calibres have dimished in different ways. This happens because the material possesses a certain longitudinal strain which is related also to the diameter (which in gut is divided into recoverable strain and non recoverable strain: in practice once a new string has been placed under tension, it no longer reattains its initial diameter at rest). This reduction of calibre will therefore also imply a corresponding reduction in working tension. It is observed that the thinner strings lengthen more and hence diminish in calibre by a greater percentage than the thicker ones (it is generally known that the thinner strings require many more twists of the peg than the thick ones). And so it also follows that, after tuning, the respective working tensions (established as identical to start with) will no longer be equal but scaled: in other words, the thinner the string, the lesser the tension.
As a result, therefore, the ‘feel’ between the strings is no longer equal (because the tensions are now different) but instead unbalanced in favour of the thicker strings. In other words, on the thicker strings more pressure from the fingers is needed to obtain the same quantity of lateral displacement as on the thinner ones.
Hence according to the laws of physics, if the tensions are not equal, nor is the lateral displacement; nor, therefore, is the feel even.
EXPERIMENTAL TESTS
As an example, we tested two gut strings of medium twist calculated to have the same tension (8,3 kg at a pitch of 440 Hz) when brought to the required pitch (the violin ‘E’ and ‘D’ in this case). The vibrating length is obviously the same for both (33 cm). We obtained calibres of .65 mm for the ‘E’ and 1.45 mm for the ‘D’ when measured at rest, i.e. not under tension. Once they had been tuned and stabilized, we proceeded to measure their diameters: the calibre of the ‘E’ had reduced to .62 mm, whereas there was no noticeable drop in the ‘D’, even when measured by a micrometer. Hence while the thinner string had dimished in diameter by 5%, the thicker string be considered as unvaried for practical purposes. These values are of an experimental type: which means that strings made in different ways may provide different percentages of reduction. The constant factor, however, is that – manufacturing techniques being equal – it is always the thinner string (i.e. the chantarelle) that contracts more. In our case the tensions of the strings stretched on the instrument reduced to 7.6 kg on the ‘E’ and 8.3 kg on the ‘D’ compared to a calculation value of 8.3 kg in both cases.
In order to have ‘E’ and ‘D’ strings that retain the kg decided on initially when tuned to pitch, one must therefore increase the initial gauge of just the ‘E’ by 5%, i.e. .68 mm. When making the traditional calculation to obtain the tensions of this second pair of strings ‘at rest’ one detects a trend of the scaled type: namely 9.2 kg for the ‘E’ string and 8.3 kg for the ‘D’. To sum up: the experiment shows that calibers of .65 and 1.45 mm lead only to a theoretical state of equal tension; conversely, if one uses diameters of .68 and 1.45 mm, once the strings have been tuned (i.e. in traction) they will assume a new, and more reduced, diameter situation, such as would exactly produce equal tension, i.e. equal feel of the XVI and XVII centuries.
This situation was in fact verified – always with the assistance of a micrometer – in a second experiment carried out on this second pair of tuned strings.
If one wants a stringing of equal feel, it is therefore necessary to use criteria of scaling when selecting the diameters of strings ‘at rest’ (i.e. not in tension). As mentioned earlier, one advantage of scaled tension is that the increasing attrition encountered when moving the bow from thin to thick strings (because of the larger contact surface) is much less noticeable.
If we respect the condition that there should be equal tension between the various strings at pitch, one concludes that scaled tension and equal tension (measured at pitch) express the same thing: equal feel.
Although the test reported in the first version of this article (in Recercare IX of 1997) produced substatially correct results, the interpretation of the data turned out to be wrong. The same consideration applies to another example cited there: that of an elastic band and steel string whose diameters were calculated to have the same tension values to start with. When tuned to the same pitch, only the elastic band will reduce considerably in section to assume a new, lower state of tension, in contrast with the unextendable steel string. At this point, therefore, the feel will be different.
Let us now turn to the cases of Serafino Di Colco and Leopold Mozart.
Di Colco writes: "Siano da proporzionarsi ad un violino le corde […] distese, e distirate da pesi uguali […]. Se toccandole, ò suonandole con l’arco formeranno un violino benissimo accordato, saranno bene proporzionate, altrimenti converrà mutarle tante volte, sin tanto che l’accordatura riesca di quinta due, per due, che appunto tale è l’accordatura del violino" (The strings are to be proportioned to the violin [...] extended, and stretched by equal weights [...]. If by touching them or playing them with a bow they form an excellently tuned violin, they can be considered well proportioned, otherwise you will need to change them as many times as necessary to obtain fifths between pairs of strings, which is precisely the tuning of the violin).
The scholar Patrizio Barbieri believes that in all likelihood these considerations are purely speculative. Mozart, on the other hand, drawing on the same concepts, suggests attaching equal weights to each pair of strings: if the diameters are well chosen, the open strings will give fifths; otherwise the diameters will need changing until that result is obtained.
-The cases of Mozart and Di Colco can lead to a certain interpretative confusion. Indeed it has been attempted to conclude hastily that they are stringings in equal tension: as if they had been worked out by ‘sitting at a desk’, so to speak, i.e. based on formulas.
Appearances, however, are misleading. The test recommended by Mozart takes place in conditions of equal weights (i.e. equal tension) that already work on the strings.
This situation therefore does not at all replicate that of apparent ‘equal tension’ obtained by means of calculation by establishing the same kg in the formula for the strings with the purpose of obtaining all the diameters of the stringing (a tension that, as we saw, will be diversified because of the differences in the thinning of each string after tuning). In his case the pairs of strings are chosen in a state of actual traction, not of calculations done on paper. Seeing that this is a situation of true dynamic equal tension (because the weight always remains the same), we therefore find that the strings also display equal feeling.
In other words, the method suggested by Leopold Mozart achieves what we indicated above, though by a different route. It is evident that the strings chosen by Mozart as suitable for the purposes of tuning in fifths would present initial diameters ‘in the packet’ that theoretically display a profile of scaled tension, exactly as in the other cases described.
-We conclude by observing that the degree of scaling mentioned hitherto does not correspond to that found in most of the historical documentation of the XVIII and XIX centuries: the tension slope is steeper. In other word, one cannot detect a situation of equal feel.
Unfortunately, at present there are no documents that can offer illuminating evidence for why this practical choice was made by the violinists of the time.
Huggins (1880 ca) advances two hypotheses: the first takes into consideration the pressure exerted by each string on the table of the instrument. He stresses that in a state of equal tension (but also of equal feeling, we add) the pressures in kg exerted by the first three strings on the underlying table are not at all equal; and this is because the angle of incidence of the string on the bridge is increasingly acute towards the thicker strings. Hence a greater thrust on the table. To obtain equal pressures on the table from every single string what is needed therefore is an ‘additional’ scaling to the condition hitherto considered. The second hypothesis considers the fact that as a rule the thicker strings are progressively more distant from the fingerboard: the result, therefore, is that in a condition of equal tension/equal feeling the fingers of the left hand must make a further effort when pressing down on the fingerboard. Hence the reduction of tension, with the aim of recovering evenness of feeling in the fingers of the left hand.
A third and final hypothesis that tends to suggest a (markedly) scaled tension concerns the search for the maximum possibile evenness of attrition vis-a-vis the bow hairs. This is propounded by Riccati already in the eighteenth century and later repeated by Pleissiard in the second half od the nineteenth century:
‘Egli è d’uopo premettere, che quantunque l’arco tocchi una maggior superficie nelle corde più grosse, nulladimeno la sua azione è costante, purchè si usi pari forza a premer l’arco sopra le corde. Questa forza si distribuisce ugualmente a tutte le parti toccate, e quindi due particelle uguali in corde differenti soffrono pressioni in ragione inversa delle totali superficie combacciate dall’arco.’ (Giordano Riccati ‘Delle Corde…’ 1760 ca)
(‘First it is necessary to say that in spite of the fact that the bow touches a greater surface in the bigger strings, its action is nonetheless constant, provided that equal force is used in pressing the bow on the strings. This force is distributed equally to all the parts touched, and hence two equal particles on different strings undergo pressures inversely proportional to the total surfaces encountered by the bow.’).
Mimmo Peruffo, 2004
MORE ABOUT OUR WOUND STRINGS
WOUND GUT STRINGS - " F " AND " A " TYPES.
- OPEN-WOUND STRINGS (demi filé) - " FD ", " AD " TYPES.
- SILK CORE WOUND STRINGS (19th C. Harps and Guitars).
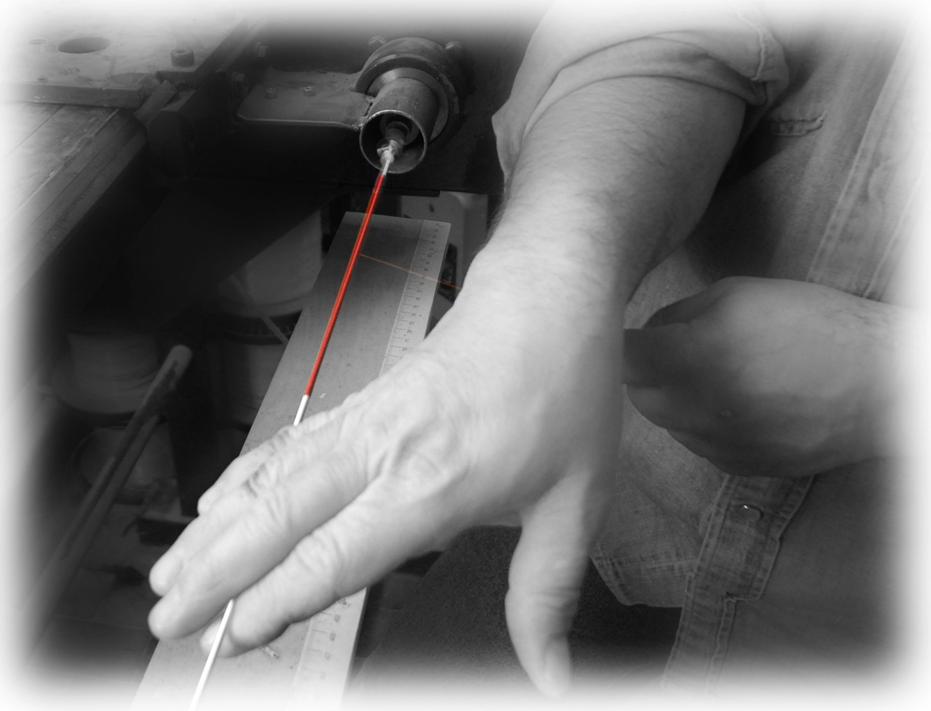
...to learn more: check at our FAQ
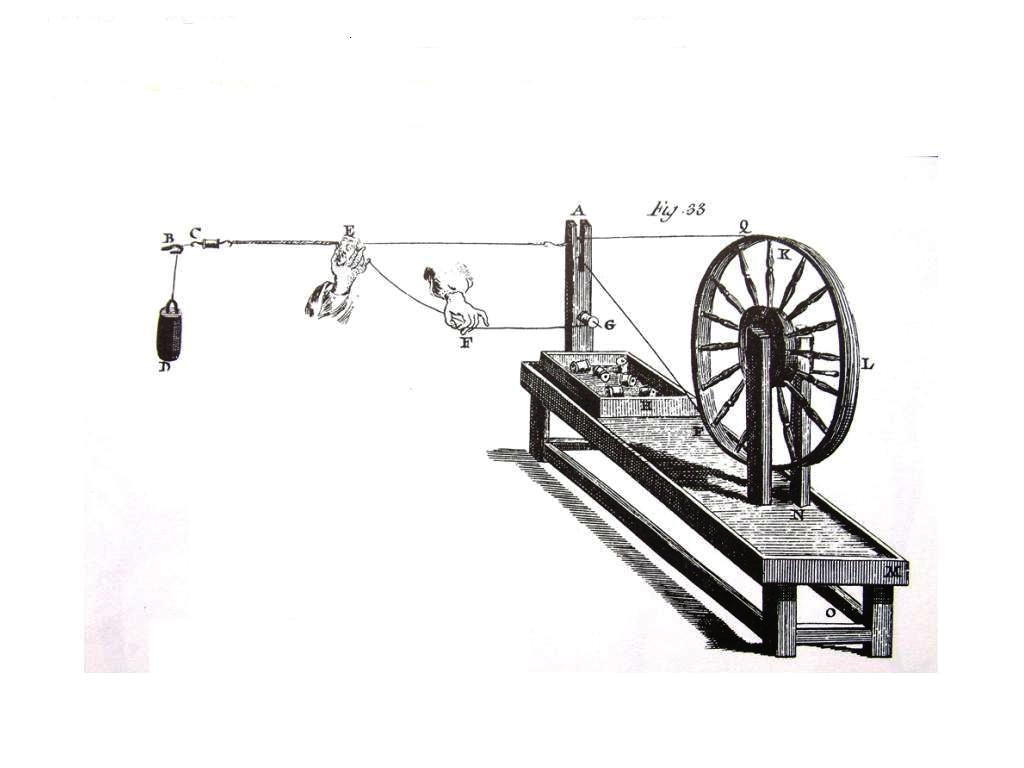
INTRODUCTION
The earliest mentions known to us of wound strings dates back to 1659 (Hartlib Papers Project; Ephemerides: "Goretsky hath an invention of lute strings covered with silver wyer, or strings which make a most admirable musick. Mr Boyle. [...] String of guts done about with silver wyer makes a very sweet musick, being of Goretskys invention”) and 1664 (John Playford: "An Introduction to the Skill of Musik...").
However, their use did not spread out very quickly for some decades: in fact the earliest iconographical evidence showing musical instruments strung with wound strings (Violin and Cello) date back to 1680.
In Italy, a country renowned for its string production, the earliest evidence is from the year 1677.
According to Rousseau (Traité de la Viole, 1685) it was the Viola da Gamba player Sainte Colombe who first introduced them into France around 1675, but the most important English Lute and Viola da Gamba tutor, Thomas Mace's "Musick's Monument", in 1676 does not mention them at all. According to James Talbot's MS. (ca.1700) Lute, Violin and Bass-Violin bass strings are still the usual gut ones, namely Lyons, Catlines or the "deep dark red" Pistoys. Only in the early decades of the 18th century wound strings -both close or open wound (called, in 18th c. France, demi-filée)- got the upper hand of traditional gut strings, revolutionizing music making to our day.
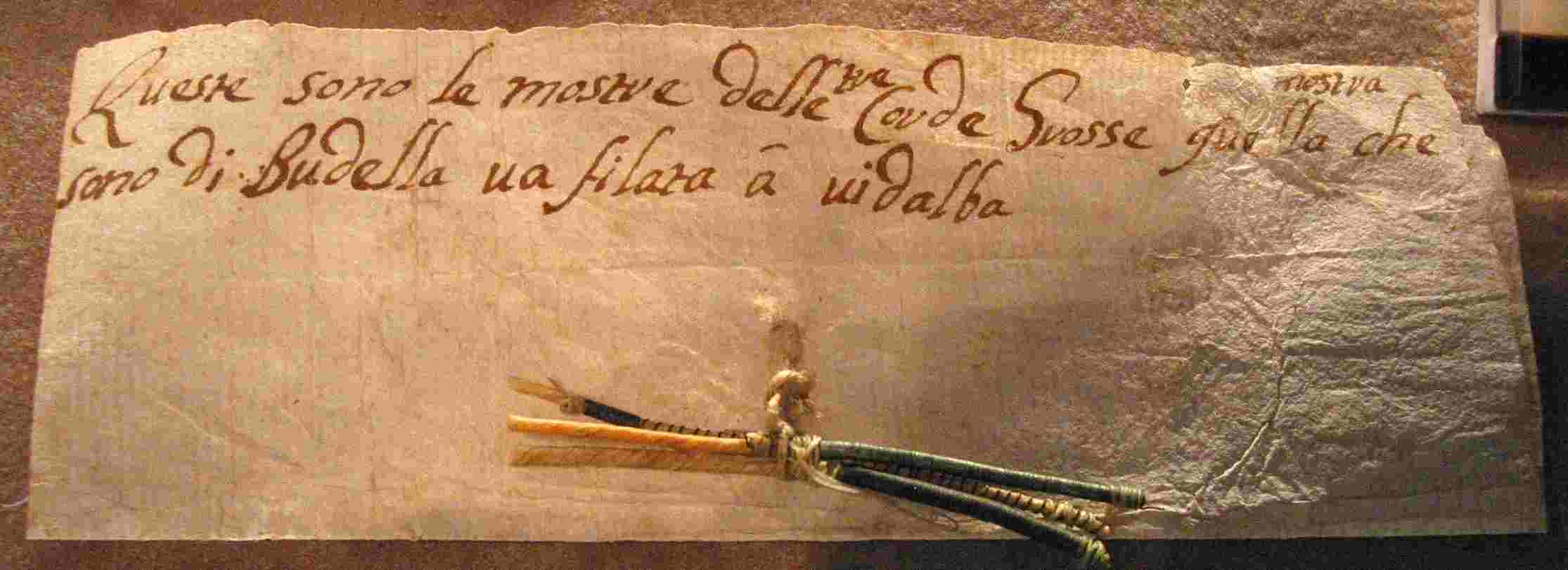
Stradivari wound strings, Museo Stradivariano Cremona
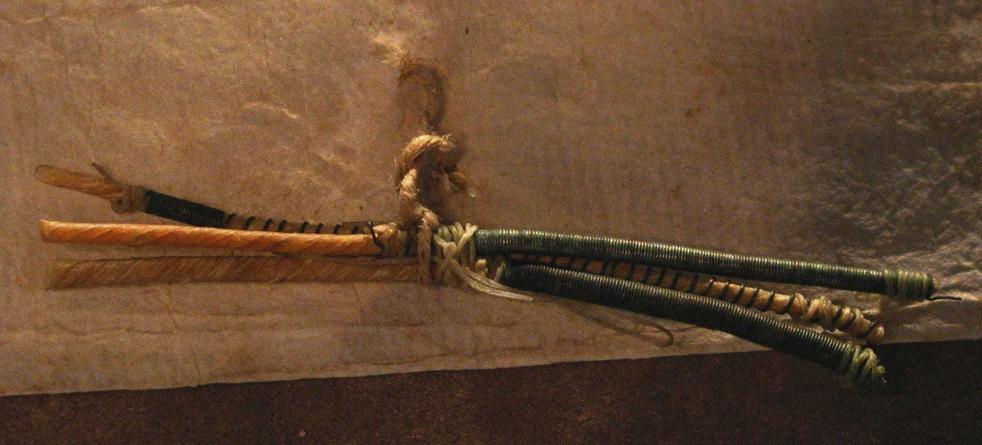
Stradivari wound strings: detail
TECHNICAL SPECIFICATIONS AND FIELD OF APPLICATION
We conceived our "F" (close wound), "FD" (open wound) in pure silver; "A" (close wound), "AD" (open wound) in silvered copper wire type-strings with the aim of recovering the typical materials and proportions of the wound strings in use in the 18th and 19th century (round wires, no silk between the metal wire and the gut-core): rather different from modern strings, as supported by historical sources and by measurements taken from original string fragments in museums.
This is our best answer to the needs of people who are seriously interested in the faithful reproduction of the musical repertories of the past.
Hereby we would also like to remind you to use our "C" type loaded gut strings when performing late 16th and hearly 17th century music; our "FD" and "AD" types on French 18th Century-repertoires (3rd D Violine; 4th Bass Viola da Gamba C); in the strictest respect to historical authenticity.
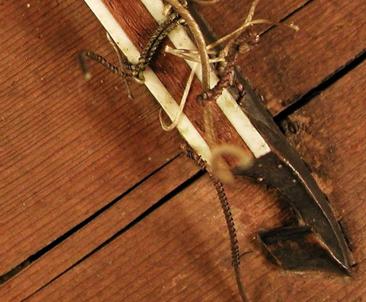
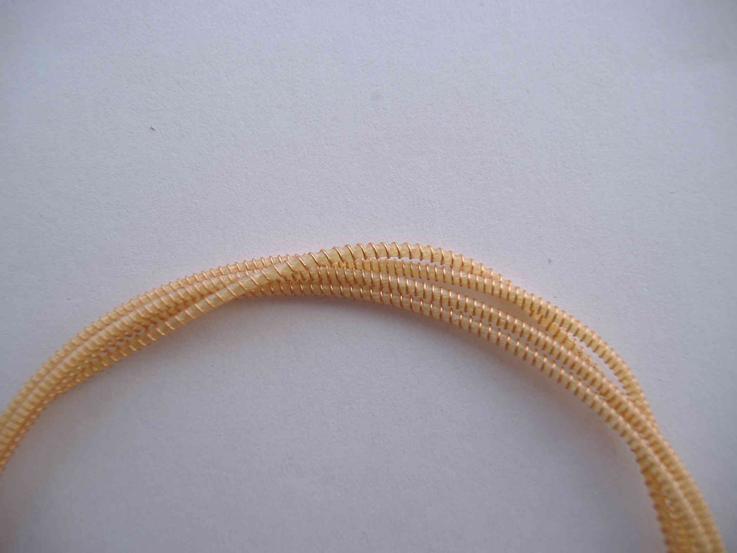
18th C. open wound bass lute strings on a Raphael Mest's lute Coming soon! Copia of the Raphael Mest's lute bass open wound strings
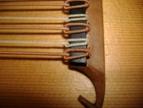
- Copia of the Raphael Mest's lute wound strings on a d- minor baroque lute -
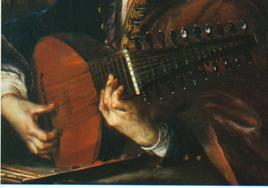
- Joahn Kupezky (1667-1740), Portrait of a luteplayer. In the original, the last bass string seem to be an open wound type -
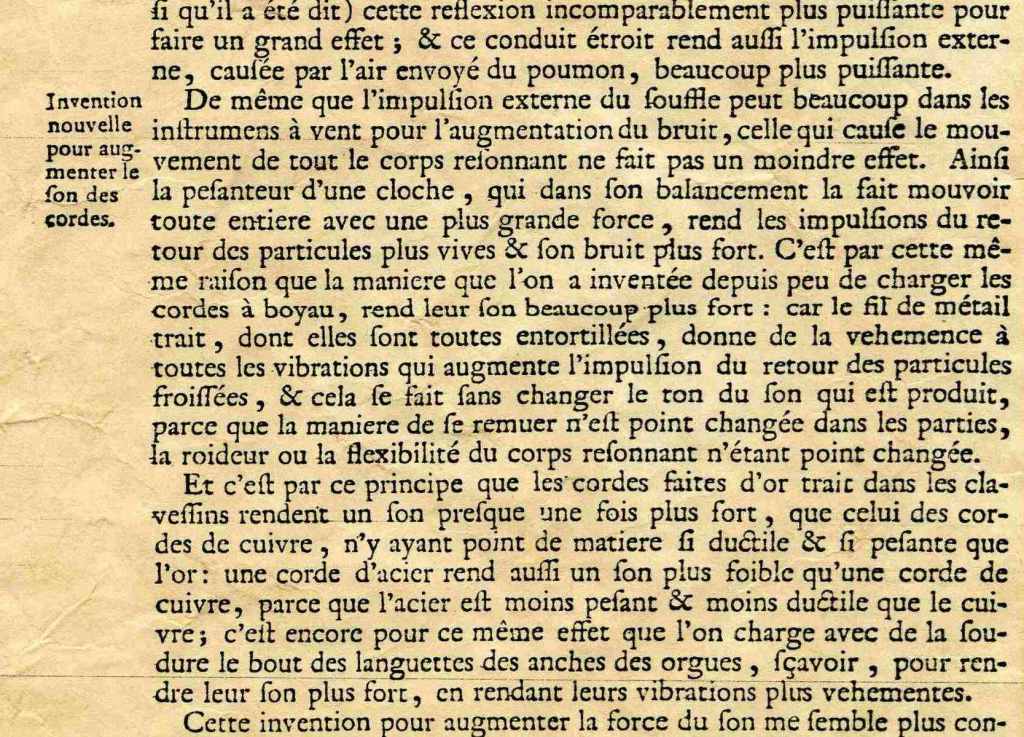
- CLAUDE PERRAULT, "OUVRES DE PYSIQUE", AMSTERDAM 1680: DETAIL -
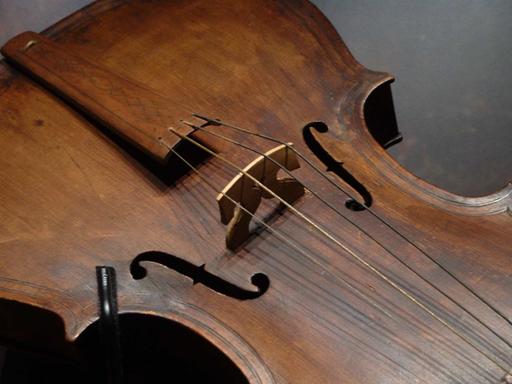
- VIOLA'S OLD WOUND STRINGS. BRUXELLES, MUSEUM ROYAL INSTRUMENTAL -
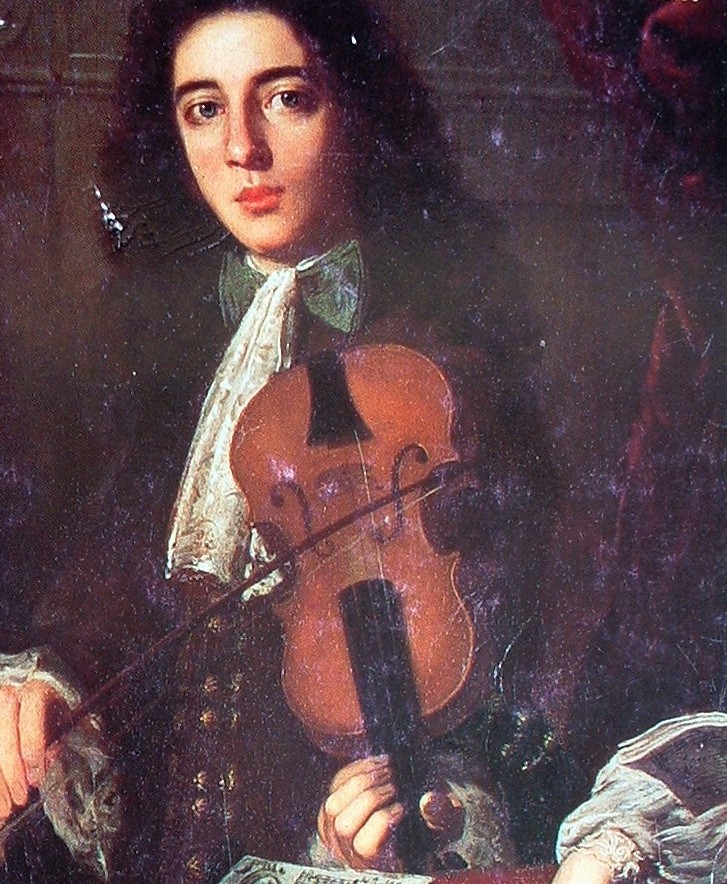
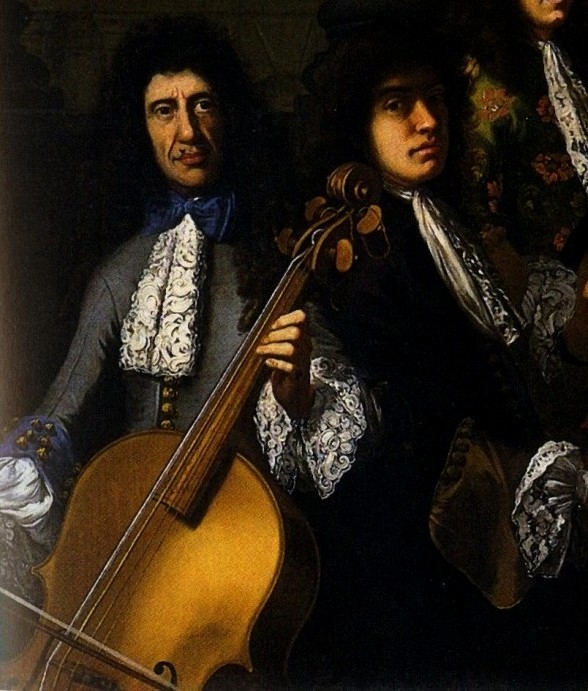
-A.Gabbiani (1685 ca.) 1st example of a 4th violin wound string- -A.Gabbiani (1685 ca.) 1st example of a 4th Cello wound string-
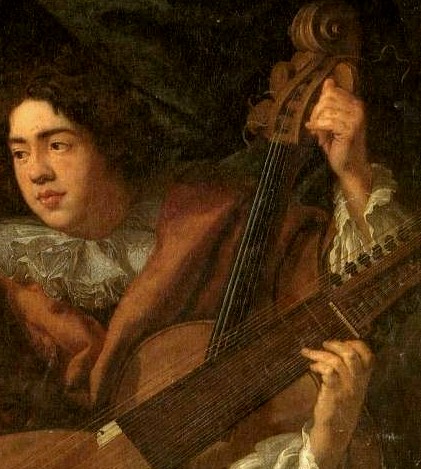
-A.Gabbiani (1687 ca.) 2nd example of a 4th Cello wound string- - F. Puget (1687 ca.): wound strings on a Bass Violin -
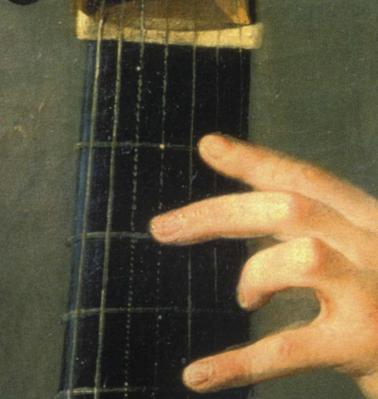
GB Forqueray 1750 ca.: detail of strings
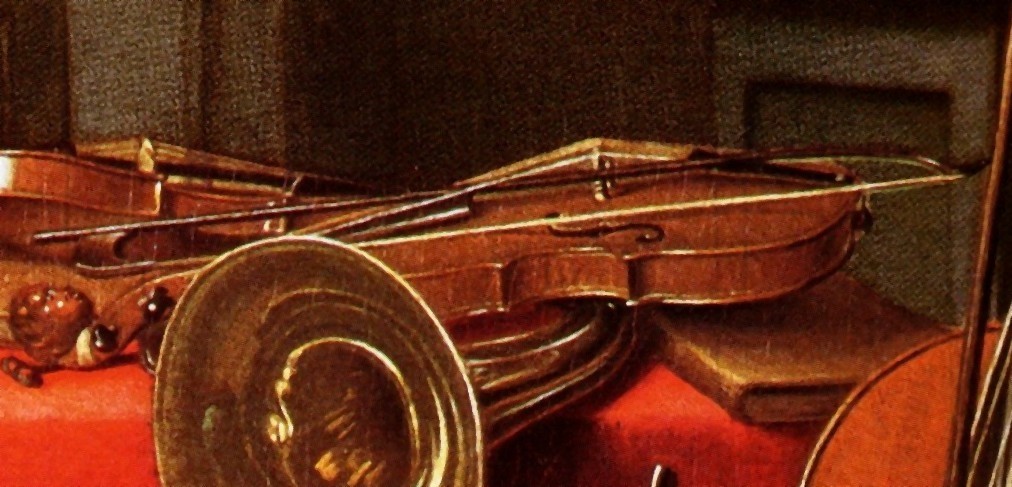
Horemans (1770 ca). detail of a violin (4th silver/silver plated wound)
ABOUT L U T E S AND BAROQUE GUITARS
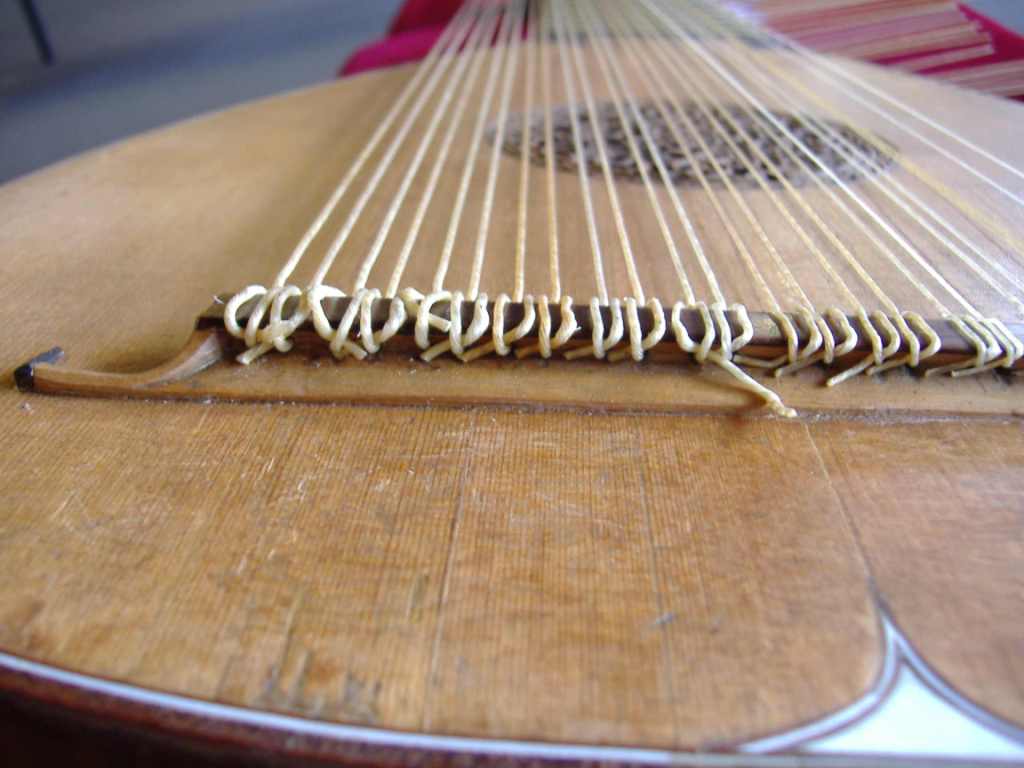
- Lute of the Germanische National Museum, Nuremberg -
Owing to the large variety of instruments within the lute family, we do not find it possible to suggest any standard stringings.
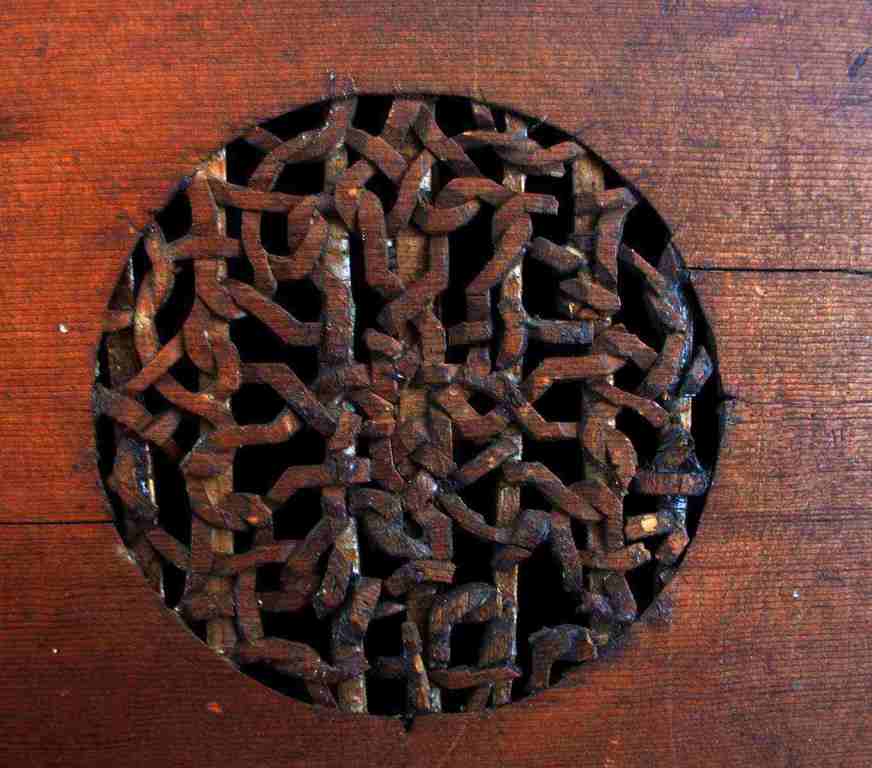
- Kremuenster's lute: detail of the rosette -
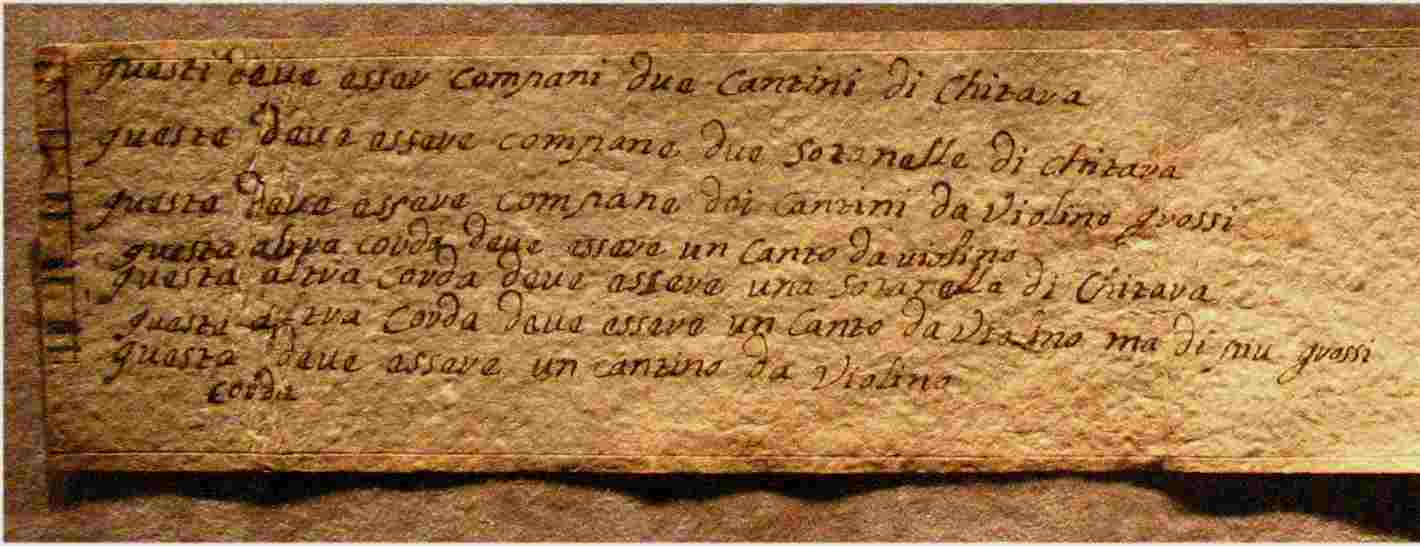
Antonio Stradivari: 5 course- guitar's stringing
- Lacking detailed information we will follow our own experience -
- For all-gut stringing on Renaissance six to ten course and Baroque eleven to thirteen course " d " minor lutes we suggest the following general scheme:
1st course: plain gut, low twist. Nylgut® strings ("NG" type).
2nd and 3rd course and all octaves: plain gut, high twist. Nylgut® strings ("NG" type).
4th course: Venice, double twist. Nylgut® strings ("NG" type).
5th to 10th course (or 13th): loaded gut ("C" type). Nylgut® wound strings ("D" type).
- For the six course-Lute / Vihuela, 5 string guitars: in respect to authenticity, we recommend the use of Venice strings for the 4th, 5th and 6th courses.
Theorbo / Chitarrone:
FRETTED COURSES.
1st and 3rd: plain gut, high twist. Nylgut® strings ("NG" type).
2nd and 4th: Venice, double twist. Nylgut® ("NG" type).
5th and 6th (and 7th, if you have one): loaded gut ("C" type). Nylgut® wound strings ("D" type).
EXTENDED BASS COURSES.
7th to 12th: plain gut, high twist. Nylgut® strings ("NGE" type).
13th and 14th: loaded gut, ("C" type). Nylgut® strings ("NGE" type).
FAQ-Aquila:
1) Why are gut strings so expensive?
2) Why did it take so long for the strings to arrive, this time?
3) From which sources do we know that the strings of the string quartet were thicker than those we commonly use today?
4) How important is, as far as quality is concerned, the colour of gut strings?
5) Is it true that strings made of ram's gut can be recognized by their (typical) brown colour?
6) Is it true that strings made of lamb's gut are better than those made of sheep's, beef’s or ram's gut?
7) Why do modern stringmakers use guts cut into strands instead of whole guts?
8) Why can't I use historical gauges on my violin/viola/cello?
9) What is the difference between a high twist and a low twist string?
10) What is a half-rectified string?
11) What care do gut strings require?
12) What care do wound strings require?
13) What is a string's quality test (so-called Mersenne test)?
14) What is a string's Breaking Index?
15) What is the acoustical lower limit of a gut string?
16) How do I measure a string's diameter?
17) How were strings sold in the past?
18) Why are gut strings sometimes varnished?
19) What benefits brings the oiling of strings, what disadvantages for the bow's hair?
20) What care should be taken with the nut and bridge grooves?
21) I checked the diameter of a gut string a noticed that it sometimes is slightly different from that declared on the string envelope: is the string faulty?
22) How should I store my strings?
23) How do I take care of buzzing in historical wound-on-gut strings?
24) How should I prepare a lute to be strung with gut?
25) What is the Working Index of a string?
26) What is Nylgut and why is it white?
27) What were typical string quartet stringings in the 18th and 19th centuries?
28) What are the technological differences between modern and historical would strings?
29) What sort of wound strings were in use in the 17th to 19th centuries?
30) Why can't we consider equal tension stringing a historical option?
31) What should I do when I put a new string on?
32) What should I do when I am not going to play for some time?
33) What is the difference between historical and modern stringing praxis (violin, viol, cello)?
34) How do I work out the right working tension?
35) Why do my strings 'whistle' under the bow?
36) Why did the string break as soon as I put it on the instrument?
37) I used a Venice string as treble: why did it break immediately?
38) I put DE type wound basses on my lute but they seem to be a bit dull compared with other wound strings. Why is that?
39) I put on my instrument a Venice type string of the same diameter as the previous high twist plain gut and it feels much slacker: why is that?
40) Is it true that in the 19th century wound on gut core strings were used on the Guitar?
41) Is true that the Guitar in the 19th century was noticeably lighter strung than today?
42) I tried some Venice type as bass strings on my Bass viol, but I am not satisfied since they sound very dull (especially the sixth does): why is that?
43) Is it true that a sharply bent string completely damaged?
44) My instrument has a 'wolf': what can I do about it?
45) I though that giving you the diameter of my wound string for replacement, but I heard that is useless: is that true?
1) Why are gut strings so expensive?
Because their manufacture is still mostly handwork and require a high degree of specialization: there are only a few of us left, worldwide, who know how to make the appropriate gut strings for historical stringing. Moreover, the whole string making process requires at least 10-12 uninterrupted days of work.
2) Why did it take so long for the strings to arrive, this time?
Probably because of one, or more, of these reasons:
- You changed, or added to, the original order.
- You ordered strings for a particular type of instrument, you did not know exactly what gauges you wanted.
- You gave an incomplete or incorrect address.
- You did not give your telephone number, which is required for carrier or express delivery in general.
- A given gauge was temporarily out of stock
- You were put on a waiting list because we had to cope with more orders than we can meet at one time.
- The mail service failed (which happens, on average, twice a month).
3) From which sources do we know that the strings of the string quartet were thicker than those we commonly use today?
Both from available historical sources we found in recent years and from surviving pieces of strings we believe to be original.
4) How important is, as far as quality is concerned, the colour of gut strings?
The colour of a gut string has no influence whatsoever either on acoustic performance or playing life.
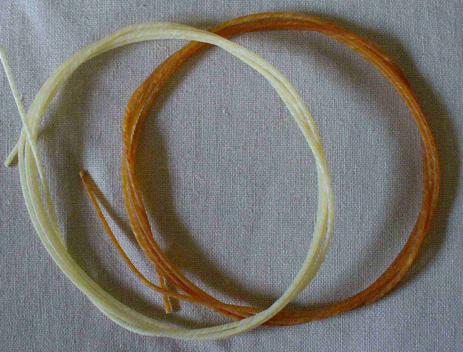
identical strings, different bleaching
Natural colour varies from gut to gut. Extremely white strings (looking like nylon) could betray too energical a bleaching, though.
5) Is it true that strings made of ram's gut can be recognized by their (typical) brown colour?
No, the gut of any animal, if unbleached, always has a more or less brown colour; in other words, such a string (in our example ram's gut) was not bleached and that was a stringmaker's precise choice.
6) Is it true that strings made of lamb's gut are better than those made of sheep's, beef’s or ram's gut?
No. A string's acoustical quality depends minly on two factors: density of the material and the elasticity.
Historical relevance apart, all these materials possess the same density (at the end of the day it is all 'dry meat').
The elasticity, on the other hand, exclusively depends on how the stringmaker produced the string (high or low twist, with the addition of hardening salts & c.).
Tests carried out with a double blind method have proven it impossible to detect any acoustical difference.
In any case it is reported that up to the mid-17th century in different italian regions the guts of sheep, lamb, wether, ram, goat, wolf, beef could be indifferently used (see A. Kircher's Musurgia Universalis, Rome 1650).
7) Why do modern stringmakers use guts cut into strands instead of whole guts?
First of all, the cleaving of gut into strands to be twisted into musical strings is a technique that was already in use in the second half the 16th century (see the roman and neapolitan stringmakers statutes from 1589 and 1653) and was certainly common in the second half of the 18th century.
The problem is that we do not know - at least not in every detail - the early steps in the historic whole gut manufacturing technique anymore.
Besides, we must point out that it is, generally speaking, nearly impossible to find lamb's gut that is so thin as to allow us to achieve a historic violin top string made of three whole guts.
In practice we always obtain noticeably thicker strings and that is a definite proof that the gut does not come from real lamb (i.e. less than one year old): hence the need to split the guts in half in order to obtain thinner strands.
On the other hand we must point out that strings made of gut strands (again, a historically correct method) are of high quality and grant a long playing life.
8) Why can't I use historical gauges on my violin/viola/cello?
There are several possible reasons:
- You haven't got used to playing with thicker strings than my usual, yet.
- Thicker strings often exert too much pressure on the sound board and that damps the sound: the pressure can be diminished by reducing the angle of the strings in relation to the bridge by way of raising the string holder at the bottom of the instrument (a solution also adopted in the past) or, if possible, reducing the height of the bridge.
To learn more: please visit this site www.damianstrings.com
9) What is the difference between a high twist and a low twist string?
A very important one: a high twist string is much more elastic and that means an increased reactivity: the string will respond more easily both to plucking and to to bowing and produce a wider dynamic excursion and timbric variety.
On the other hand a low twist string, being stiffer, is less reactive but more resistant under stress and thus suitable for all trebles in general.
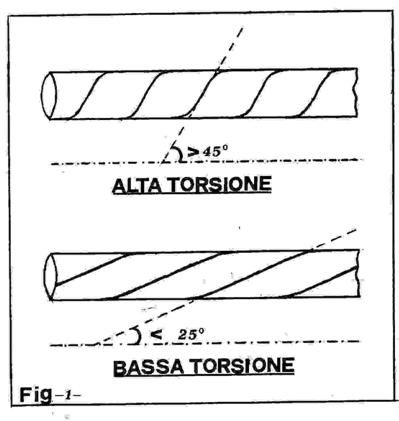
Low and high twist
The material being the same, elasticity and resistance are inversely proportional and that is why it is not possible to use high twist strings as trebles, since they would easily break.
Low twist strings are best suited for Trebles - but not best suited for the mid-register strings, where the acoustic performance would be impoverished.
10) What is a half-rectified string?
Modern gut strings are machine -polished to a perfectly smooth surface, which inevitably damages the surface fibers.
With half-rectified strings the polishing process is stopped before a completely smooth surface is obtained.
Thus it is possible to imitate the hand polishing of the past and also the surface fibers remain mostly intact.
This results in a longer playing life, better keeping in tune and better acoustc performance (broken fibers have a damping effect on the sound).
11) What care do gut strings require?
No particular care.
But in the case of the Doublebass it is advisable to treat the length of the string subject to the action of the left hand with deer fat.
This will extend their playing life.
Lacking deer fat, booth grease will also do successfully tested.
12) What care do wound strings require?
No particular care.
Should the core, under exceptionally cold or dry climatic conditions, buzz inside the winding, the string can be treated with olive or almond oil.
13) What is a string's quality test (so-called Mersenne test)?
In the past it was used to tell a good string from a false one. you pull a string taut, one end in each hand, and you pluck it repeatedly with one finger, carefully watching the cone of vibration.
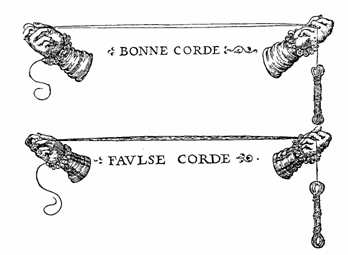
The Mersenne's test
The cone of vibration must be regular and sharp at the outer sides and free from fuzzy lines in the middle.
This test was commonly done because the hand polished strings allowed for gauge irregularities along the finished string.
Today, thanks to modern rectification, this test is generally unnecessary.
14) What is a string's Breaking Index?
The Breaking Index is the higher frequency a gut string of any diameter can reach at a string length of 1mt.
For both gut and Nylgut a mean value of 260 Hz.mt is a good reference parameter.
In other words, a 1 meter long string - gut or Nylgut - will statistically always break at 260 Hz, i.e. about 'C'.
Hence we deduce that the product of the pitch of the treble and by the string length (more properly called 'Working Index') must always be below this value, under pain of immediately breaking the string at values over 260 or a very short playing life at values between 240 and 260. No problems below 240.
What is its practical use?
Example: can I tune in A 440 a lute with a string length of 62cm?
.62 mt (62cm) x 440 (Hz) = 272.8 Hz.mt
The answer is: no, I can't.
What should the appropriate string length be?
A safe index should not exceed the 240 value.
So: 240/440 Hz = .545 mt.
In practice the appropriate string lengt (at A-440) should not exceed 54 cm.
Rule of thumb (assuming the system bridge-string-nut is free from any so called 'cutting effect'):
- Working index within 240: green light.
- Working index between 250 and 260: amber light (the treble could break in a few hours/days, especially by high humidity).
- Working index over 260: red light (the treble will break immediately or within minutes).
Because of the lack of the instrument size standardization, it is important to verify whether medieval lutes and harps satisfy these values, but also where exact copies of original instruments, lutes first of all, are concerned - original string lengths were optimized for the pitches used by the customers of the time, and the pitches commonly in use today are usually higher.
15) What is the acoustical lower limit of a gut string?
It's the maximum diameter able to produce an acoustic performance which is generally regarded as (still) acceptable to our ears (in other words, its inharmonicity level).
This limit is empirical and is above all a function of the string- elasticity.
Other relevant factors are string length, whether the string is bowed or plucked, quality of the instrument and working tension.
Here, too, it could be express in terms of Acoustic Quality Index, i.e. the product of string length by frequency.
Empirically we can say that on a mean size g- tuning lute (60-62 cm s.l. nowdays) a 1mm high twist string (5th course) is dull to the point of requiring an octave.
A diameter of 1.40 mm (6th course in a G tuning - Lute) is the lower acceptable limit for a double twist string (Venice type).
On bowed instruments this limit can empirically be increased by a factor of 1.10.
What is its practical use?
It is useful in deciding, when we calculate our diameters, when we have reached the point where we should switch from a plain gut, Nylgut or Nylon string to a wound one.
Rule of thumb:
- Acoustic Quality Index below 100: a gut/Nylgut/Nylon string begins to lose its acoustical quality (e.g. on a Lute we need octaves).
- Acoustic Quality Index below 80: we need to switch to a wound or loaded string.
16) How do I measure a string's diameter?
Today you can do it with a high-precision micrometer.
One must zero it exactly and be careful not to squash the string while measuring to avoid false readings.
And in the past?
From about 1830 into the mid-20th century they used a gauge (the first description of one is in Luis Spohr's Violinschule, Vienna 1832).
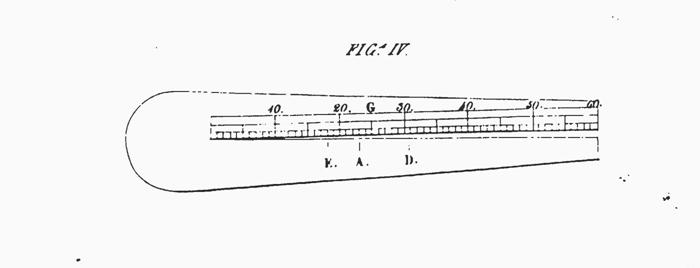
Louis Sphor’s string gauge, 1832
Luis Spohr's gauge is a metal plate with an acute ‘V’ with gauges scored on the edges: the string slid in until it touches both sides of the V. at this point we read its gauge value.
This method, obviously, allows for a certain margin of approximation. We have no record of similar methods being used in the 18th century.
Marin Mersenne (Harmonie universelle, Paris 1636) suggests winding the string around a small cylinder a given number of times, measuring its length and dividing by the number of spires.
17) How were strings sold in the past?
Present string gauging is a relatively modern praxis, adopted after the introduction of precision mechanical polishing.
Up to the beginning of the 20th century a string's diameter was first of all determined by the number of guts employed to manufacture it. a violin treble, for example, was generally made of three guts.
This means that, gut being a non-standardizable natural product, the resulting string was not of a constant diameter but fell within a possible diameter bracket.
In our violin example the string obtained with three whole lamb guts would have a diameter of between .65 and .75 mm, most probably .68-.70 mm.
Strings were usually sold in oiled envelopes containing 30 to 50 strings, all made of the same number of guts: first of all the musician had to select the true strings from the false ones - see 'Mersenne's test - and then select with a gauge and put aside the ones that were too thin or too thick for his purpose.
18) Why are gut strings sometimes varnished?
Gut strings are varnished in order to protect the strings from wear and tear.
The varnishing of strings is not a historical process; the earliest samples of varnished strings we have found only date back to the 1920-30s.
A varnished string has a somewhat duller sound and the attack under the bow is slightly more difficult and liable to 'whistle'.
19) What benefits brings the oiling of strings, what disadvantages for the bow's hair?
Oiling is the last step in the string manuifaturing process and makes the string more stable to humidity changes.
After a protracted immersion in oil - the coiled string is kept in oil for at least one month - the string develops a longer playing life and a better acoustical performance.
The oils traditionally employed were olive or almond
Notice! clean the string carefully with an appropriate solvent before putting it on the instrument: any oil leftovers can contribute to make the bow 'whistle'
20) What care should be taken with the nut and bridge grooves?
A large number of strings break because of the cutting effect of sharp edges on bridge and nut.
Thomas Mace in 1676 advises: ‘take a knife and make a little impression upon the nut ... [which] must afterwards be filed down deep enough for the string to lye in ... after you have marked the places for all strings to lye in, which may be done with a pencil or pen and ink ... you must take it [the nut] and polish it very well (but especially the notches) ... take a piece of new neats-leather and a little scraped chalk wet in spittle, which with good pains must be rubbed so long till ... the notches be very smooth’.
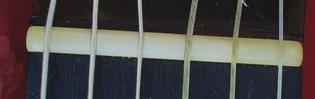
the well executed grooves in a nut on a guitar by Antonio Torres
All sharp edges and angles must be accurately eliminated.
Only after this operation apply some soft pencil lead or very dry soap to the groove. this will not only help tuning and keeping in tune but also prevent the string from squashing and jamming in the groove, increasing the probability of breakage. Robert Dowland, in his ‘Varietie of lute lessons’, London 1610, suggests:’ ...when you set them on the instrument they will sticke (and rise by starts) in the nut, and there breake, even in the tuning: the best remedy when the strings sticke so, is tu rub the little nickes of the nut (in which the strings slide) with a little oyle, waxe, or black lead’.
21) I checked the diameter of a gut string a noticed that it sometimes is slightly different from that declared on the string envelope: is the string faulty?
No, gut is an extremely hygroscopic material and the amount of humidity absorbed can slightly alter the string diameter. on humid days a string will probably present a slightly thicker diameter, on dry days a slightly thinner one.
Practical tests show that a .82mm string on a humid day can measure .84, or .80 on a particularly dry day.
The diameters shown on our string envelopes refer to a standard condition of 20°C and 60% relative humidity.
Such variations influence the string working tension only minimally.
22) How should I store my strings?
The main enemy of gut strings is humidity: keep them in plastic envelopes or in air tight boxes. A carefully stored string will keep its quality for many decades.
23) How do I take care of buzzing in historical wound-on-gut strings?
Historical wound strings, lacking a damper betweeen core and wound wire, in particularly dry climate may present this problem.
Tutors of the past (e.g. Friedrich Dotzauer's ‘Méthode de violoncelle', Paris c. 1830) suggest lightly wetting the whole string with a few drops of olive or almond oil in order to have the gut core swell lightly and make full contact with the winding again.
Never use water!
24) How should I prepare a lute to be strung with gut?
Making sure there are no sharp edges anywhere where they may cause a cutting effect (nut, bridge, string holder - see faq 20).
The length of string winding on the peg shold be as short as possible, avoiding any overlapping spires (which affect the tuning stability) and squashing and jamming the string against the pegbox side (see Thos. Mace's Musick's monument, London 1676).
25) What is the Working Index of a string?
The ‘Working Index’ is the product of string legth (in mt.) multiplied by treble pitch (in Hz) and indicates whether the chosen string length is right for the intended tuning.
In other words (see faq 14) whether we risk breaking the treble (when the string length is too long) or a poor sound quality (too short strings produce a duller sound).
On lutes and violins it is advisable to keep the Breaking Index in the 230-240 Hz x mt bracket, with the treble working close to its breaking point and granting the best possible sound in the bass register.
26) What is Nylgut and why is it white?
Nylgut is a synthetic material we discovered and copyrighted in 1997: it has the same mean specific weight as gut and a low degree of humidity absorption - ony 10% that of nylon.
We could even call it 'synthetic gut'.
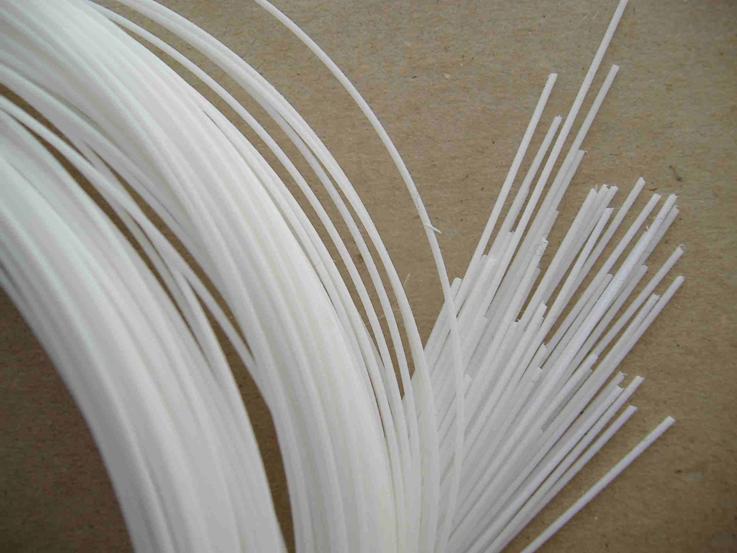
Nylgut strings
In theory a gut string and a Nylgut one should have the same diameter.
But since nylgut is quite 'stretchy' we advise using a slightly thicker diameter.
Pull carefully but resolutely and repeatedly the string with your fingers while tuning it for the first time (see faq 31).
Concerning the 'cutting effect' follow the suggestions given for gut strings at faq 20.
The white colour is simply a commercial choice, an image.
Because of its particular colour the strings catch immediately the eye both in concert and on CD covers, magazines, websites or TV. And that is good for business.
Unfortunately, because of the bow 'slips' on it, Nnylgut cannot be used on bowed instruments.
27) What were typical string quartet stringings in the 18th and 19th centuries?
This is a fairly vast topic and we suggest this further reading.
In a nut shell:
-Violin: gut for the three top strings, wire wound on gut for the fourth.
A wound third is historically incorrect.
Although in the 18th century and exclusively in France an open wound D string was used, which in the 19th century was substituted with plain gut.
-Viola: gut top two strings, wound third and fourth.
-Cello: until ca. 1730: gut top three strings, wound fourth; wound third and fourth afterwards.
-Three string Doublebass: gut top two strings, third either plain gut or wound.
-Four string Doublebass: as above, wound fourth.
Here we must point out how modern wound strings (flat metal winding on a rather stiff gut core; silk padding between gut core and metal winding; different, metal biased, gut core to winding ratio from that of historical strings) heavily change the real expressive qualities of historic stringings.
28) What are the technological differences between modern and historical would strings?
Historical wound strings present the following general features:
- low or high twist gut core.
- round metal wire winding.
- no silk 'padding' between core and metal winding.
- metal wire of silver, silvered copper, plain copper or its alloys (brass).
- different gut/wire ratio than the modern wound strings.
lengths of wound strings from the18th century
Modern wound strings:
- flat metal winding.
- stiff, low twist core.
- silk 'padding' between core and metal winding.
- employment of modern alloys like tungsten, nickel, &c.
- metal-biased gut/wire ratio.
Hence the acoustical differences are quite noticeable and interest both dynamic and timbric aspects.
29) What sort of wound strings were in use in the 17th to 19th centuries?
Three sorts:
- Close wound: the single wire spires are tightly wound touching one another. It is the still commonly used sort.
- Double wound: a second close wound layer is laid over the first one.
Because of the large quantity of metal wound on the gut core they were employed on instruments with a short string length but requiring a low tuning, e.g. violoncello da spalla, 5th double bass string &c.
- Open wound: the single wire was wound so that the spires would not touch one another but with a space in between equal or slightly wider than the wire diameter (see F. le Cocq, Paris 1724); these strings were in use exclusively in the in 18th century as transition between plain gut mid-register and close wound basses, e.g. Bass viol 4th, violin 3rd &c.
30) Why can't we consider equal tension stringing a historical option?
The concept of equal tension as expressed in equal number of kg is modern one, probably making its first appearance about 1860 (Maugin-Magne, ‘Nouveau manuel complet du luthier’).
Up to the mid-18th century the tension of a string was exclusively understood in terms of feeling of stiffness to the touch, which is something different from the way we understand it today.
While the amount of tension is solely expressed in kg, a feeling is conditioned by a number of parameters, such as string length (this is why theorbo- diapasons, if tuned with exactly the same tension, feel so much more slack than the fretted strings), type of string and diameter.
In a set where all the strings are calculated with the same tension in mind will feel quite different to the touch: this contradicts the criteria of the 16th and 17th centuries, which require that all strings present a homogeneous feeling under the fingers.
In conclusion, the string type being equal, a set of string, in order to present a feeling of equal tension, must actually have an scaled tensions.
Click here for further details.
31) What should I do when I put a new string on?
Once checked that all points of contact are smooth and free from sharp edges, when tuning a string for the first time, pull it with your fingers until it stays in tune: moderately the trebles and wound strings but with a bit more energy the thicker ones.
This applies to both gut and synthetic strings, especially to Nylgut:
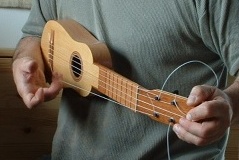
32) What should I do when I am not going to play for some time?
Follow Thos. Robinson's advice (begin of the 17th century) and tune the treble a bit lower, thus reducing string-stress.
33) What is the difference between historical and modern stringing praxis (violin, viol, cello)?
Quite a substantial one: research on historical sources and observation of surviving pieces of original strings point to the use of not only thicker than commonly in use today, but also hand polished (hence not perfectly smooth) strings.
Now, choosing to use historical string diameters can sometimes lead to a readjustment of the instrument's set up - especially concerning the angle of the strings on the bridge - which sometimes the instrument itself does not accept very willingly.
This is why beside a historical stringing (which we always find desirable) we also propose a modern one (in light, medium and heavy grading).
34) How do I work out the right working tension?
Finding the right working tension for each instrument is basically an empirical process, depending on tipe of instrument, type of string and personal musical attitude.
In other words, there are no specific mathematical furmulae for it.
What we do suggest is: put a 2nd or 3rd string on the instrument of a diameter you consider adequate (bowed or plucked, the process is the same).
Tune the string to the wanted pitch and check whether it feels too slack or too taut according to your own perception.
Lower or raise the pitch by as many semitones as necessary to bring it to the right tension, that is to the point where it feels right to you, neither too slack not too taut.
Now apply the following indications:
-The string was originally too taut: multiply its diameter by .944 by the number of semitones by which you decreased the starting pitch (.944 reduces a given diameter by a semitone).
-The string was originally too slack: multiply its diameter by 1.059 by the number of semitones by which you raised the starting pitch (1.059 increases a given pitch by a semitone)
Example: I put an .82 third string on my lute (or any bowed instrument) and it feels too slack.
Solution: starting from the string tuned at the wanted pitch, raise it semitone by semitone until the tension feels subjectively right.
Let us suppose you raised it by two semitones: multiply 82 by 1.059 twice: the diameter you want is 91.9(6) mm, i.e. a 91 available as standard on the market.
35) Why do my strings 'whistle' under the bow?
There can be several causes, sometimes more than one at once.
A very common one are oil leftovers from manufacturing: clean them carefully with a rag damped with ‘white spirit’.
36) Why did the string break as soon as I put it on the instrument?
There are three possible reasons:
- The string is faulty.
- The string length is too long (exceeding the Breaking Index).
- Some point of contact between string and nut, bridge or string holder has a sharp edge or is lacking appropriate lubrication (i.e. pencil-graphite etc.).
- Faulty string: generally it does not break cleanly but through progressive fraying, usually announced by little hairs raising along its length.
- Excessive string length: check whether the product string length by frequency is in excess of 240, regardless of type of instrument: lute, baroque guitar, fiddles and medieval instruments in general.
- The cutting effect of sharp edges usually results in a sudden and clean break. It can also be caused by nicks in the string, as consequence of careless.
Notice: the string breaks under tension: if the damage took place at the nut edge, for instance, the breakage will seem to correspond to, say, the second or third fret, since the string is no more under stress. likewise, if the damage took place at the bridge, it will seem to have broken somewhere between it an the string holder.
37) I used a Venice string as treble: why did it break immediately?
Venice strings possess a high degree of elasticity, noticeably more that a high twist string.
But being elasticity and resistance to stress inversely proportional this type of string should not be used where the Working Index (i.e. the product of string length by frequency) exceeds 140Hz x mt (which generally is the working index of treble strings).
38) I put DE type wound basses on my lute but they seem to be a bit dull compared with other wound strings. Why is that?
DE wound strings were conceived with the purpose of filling in a gap in the area of bass strings for short extention archlutes and swan-neck baroque lutes.
The ratio nylgut core / metal winding is core biased, in order to counterbalance the typical sound of regular wound string, characterized by a very long sustain, rich in overtones and poor in fundamental. in other words a bit too guitar-like.
On the other hand DE wound strings on fretted courses are quite fundamental-heavy and require the use of octaves. Like in the old times, in fact. The core bias is aimed to recreating the sound of our loaded gut basses.
39) I put on my instrument a Venice type string of the same diameter as the previous high twist plain gut and it feels much slacker: why is that?
According to the string formula two strings of the same material and same gauge, string length and pitch being equal, will also have the same working tension provided the diameter remains the same also under stress.
But in practice this happens only if the strings are also manufactured in the same, identical manner.
In other words they must stretch by same amount under the same stress, thus reducing their diameter by the same amount (empirically proven by the same amount of peg turns needed to tune them).
Because of its nature a Venice string stretches noticeably more than a regular high twist string, which leads, under equal stress, to a somewhat thinner diameter.
Hence the necessity to use a thicker starting diameter: under working stress it will settle to a diameter similar to that of a regular string's and will eventually lead to the same working tension.
In practice the correct diameter of an equivalent Venice string is obtained by multiplying the plain high twist string diameter by 1.10.
40) Is it true that in the 19th century wound on gut core strings were used on the Guitar?
No, historical evidence has proven that both six course (in late 18th and early 19th centuries Spain) and six string guitars were only strung with wound on silk basses. silk was used until nylon multifilament was introduced about 1950s.
41) Is true that the Guitar in the 19th century was noticeably lighter strung than today?
No, presently available evidence (with particular reference to the tutors of Sor, Carulli and Aguado) shows that the same diameters were used as on the violin; string tensions are practically comparable to those of the modern classical guitar.
The one exception is the 19th century neapolitan guitar (Fabricatore, for example): some documents point to tensions slightly lighter than on the violin.
Besides, the tension profile was less scaled than commercially available guitars sets suggest today.
We advise to always carefully check whether the bridge is soundly glued in place before stringing an original guitar with a modern string set.
42) I tried some Venice type as bass strings on my Bass viol, but I am not satisfied since they sound very dull (especially the sixth does): why is that?
This is a fairly frequent problem and is generally not to be blamed on the strings. the main cause is that the instrument's string length is too short for the required pitch if you intend to string your instrument entirely with gut.
Before the adoption of wound strings - which made their first appearance in the second half of the 17th century - the Gamba family had noticeably longer string lengths than those commonly in use today.
From Pretorius' tables we can calculate exactly that the bass viol had a string length of c. 85cm ('Syntagma musicus', Wolfenbüttel, 1615-20) against the 68-70cm commonly in use today.
Likewise modern tenor viols have 55-56cm against the 58-62 which were common in the late 16th / early 17th centuries.
Historical instruments were designed with a longer string length in order to have the trebles work close to their breaking point (Working index not lower than 220 Hz x m - see faq 14).
This was the only way to grant every string the minimum diameter possible, basses first of all.
In fact string length and diameter are inversely proportional.
Reducing a string's diameter (tension being equal, of course) is always beneficial to the quality of sound and bow attack.
Exactly what basses, the most problematic of all strings, need.
If, on the other hand, the strings length is reduced they will have to be thicker, which will negatively influence the sound quality because of the string's increased inner damping coefficient ('inharmonicity' index).
Solutions to the problem?
Basically three:
1) Use instruments with string lengths typical of the period preceding the appearance of wound strings, i.e. 82-85cm for the Bass, c. 61 for the Tenor and c. 41 for the Treble (see proportions in Thos. Mace's Musik's monument, London 1676).
This way gut strings will give an excellent, prompt sound.
2) If possible (i.e. if the bridge height allows), move the bridge towards the base of the 'C' cuts, thus increasing the string length and improving the acoustical performance in general (do remember to calculate the string diameters keeping this added factor in mind).
3) Employ wound strings (but only in case a more appropriate instrument is not available or you are not willing to lower the bridge position - which is a historically correct trick).
43) Is it true that a sharply bent string completely damaged?
A gut string that has been sharply bent shows a whitish 'nick' at the bending point.
This indicates a slight loss of fibre cohesion but does not mean at all that the string was damaged. The string is still perfectly intact. Signs of serious damage are:
a) the string has been indented
b) the fibres became untwisted to the point of coming apart and the string is not cylindrical anymore.
44) My instrument has a 'wolf': what can I do about it?
Try knotting the string the way the ancients did:
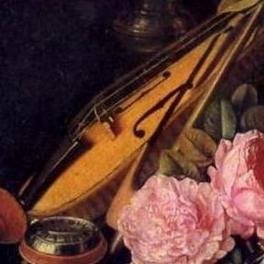
Unfortunately there is no exact procedure about it, you simply have to try experimentally with each string.
To be avoided with wound strings, tholugh!
45) I though that giving you the diameter of my wound string for replacement, but I heard that is useless: is that true?
Yes. Knowing the diameter is useful for strings made of only one material, like plain gut, Nylon, Nylgut or any metal.
Wound strings are composed of different materials and so they can be defined according to the following parameters:
a) 'Equivalent Solid Gut'
b) 'Metallicity Index'
- Equivalent Solid Gut: since wound strings are made by coupling different materials we decided to define them in terms of equivalent solid gut: in practice we refer to the diameter of a theoretical gut string possessing the same weight per unit of length as the wound string in question. For the same pitch and string length we'll thus have the same working tension. And this is important to work out our string diameters.
How can we work out the ‘equivalent solid gut’ of a wound string we want to replace and we know nothing about?
Answer: we weigh the string on a scale reading weight in grams and we measure the length of the string. We then divide the weight in grams by the length in meters and then take the square root of the result: that will give us our equivalent in millimeters.
Example: the wound string weighs 35.5g and is 98 cm long: 35.5g/0.98 m = 36.22, whose square root is 6.05. In practical terms our wound string is equivalent to a 6mm thick plain gut string.
- Metallicity Index: the same equivalent solid gut can be reached by numberless percentage relationships between gut and metal. Obviously increasing the one implies decreasing the other by the amount that is necessary for keeping the weight of the string, i.e. its equivalent solid gut, constant.
The higher the gut component, the duller will the sound tend to be, the higher the metal component the brighter the sound. So the 'correct' metal-to-gut ratio mainly depends on the particular timbric/dynamic mixture any given combination can produce and is subjectively felt as 'aesthetically pleasing'.
In other words, there is no objective formula in deciding what the right mixture is. Once decided what the gut equivalence, i.e. the correct working tension, of a string should be, the ratio metal to gut can only be worked out through experience.
The Metallicity Index is also connected with the position of the string on the instrument. The third string on a cello must clearly have a lower Metallicity Index than the fourth, which must have a higher percentage of metal in order to compensate the loss in brightness caused by the lower Acoustic Quality Index for such string position (see Q 15).
Two strings of the same gut equivalent value can possess a completely different Metallicity Index.
Let us take, for example, the third string of both a viola da braccio and a cello.
On the viola da braccio C we will find a noticeably higher Metallicity Index than on the cello G. And this is why we cannot use a cello G in place of a viol C: the working tension might even turn out to be correct, but the acoustical result will be completely unsatisfactory.
Vivi felice
Mimmo Peruffo 2007
Conversion tables
Nylgut gauges |
Nylon gauges |
Carbon fibre gauges |
36NG |
40 |
30 |
38NG |
42 |
32 |
40NG |
44 |
34 |
42NG |
46 |
36 |
44NG |
48 |
38 |
46NG |
52 |
40 |
48NG |
54 |
40 |
50NG |
56 |
42 |
52NG |
58 |
44 |
54NG |
60 |
46 |
56NG |
62 |
48 |
58NG |
64 |
50 |
60NG |
66 |
52 |
62NG |
68 |
52 |
64NG |
70 |
54 |
66NG |
73 |
56 |
68NG |
73 |
58 |
70NG |
76 |
60 |
73NG |
79 |
62 |
76NG |
85 |
64 |
79NG |
88 |
68 |
82NG |
91 |
70 |
85NG |
94 |
73 |
88NG |
97 |
76 |
91NG |
100 |
79 |
94NG |
104 |
79 |
97NG |
/ |
82 |
100NG |
/ |
85 |
104NG |
/ |
88 |
Pyramid gauges |
Aquila equivalents |
905/1013AL |
73D (wound nylgut) |
906M/1014AL |
76D |
906 |
79D |
1006/10065 |
82D |
9075 |
85D |
908/1007 |
88D |
1008/10075 |
91D |
909/9085 |
94D |
1009/10085 |
97D |
10095 |
100D |
1010 |
104D |
1011 |
108D |
10105 |
112D |
1012 |
116D |
1013/1014 |
120D |
- |
124D |
1015 |
128D |
1016 |
132D |
- |
136D |
1017 |
140D |
1018 |
145D |
1019 |
150D |
1020 |
155D |
1021 |
160D |
1022/1023 |
165D |
1024 |
170D |
1025 |
175D |
1076 |
180D |
1027 |
185D |
1028 |
190D |
1029 |
195D |
1030/1031 |
200D |
1032/1033 |
210D |
1034/1035 |
220D |
1036/1037 |
230D |
1038 |
240D |
1239 |
245D |
1240 |
250D |
1440/1441 |
260D |
Millimetres |
Thousanths |
.10 |
4 |
.15 |
6 |
.20 |
8 |
.25 |
10 |
.30 |
12 |
.35 |
14 |
.40 |
16 |
.45 |
17.5 |
.50 |
19.5 |
.55 |
21.5 |
.60 |
23.5 |
.65 |
25.5 |
.70 |
27.5 |
.75 |
29.5 |
.80 |
31 |
.85 |
33 |
.90 |
35 |
.95 |
37 |
1.00 |
39 |
1.1 |
43 |
1.2 |
47 |
1.3 |
51 |
1.4 |
55 |
1.5 |
59 |
1.6 |
63 |
1.7 |
67 |
1.8 |
71 |
1.9 |
75 |
2.0 |
79 |
Varnished or Natural Strings?
Since we have started offering the option of varnished strings we have received many questions about the advantages of purchasing the varnished rather than the natural strings.
When we varnish strings we put on three coats of a special varnish that we have found stretches with the gut.
The answer depends a little on your own circumstance: how you play, your environment and the acid content of your perspiration.
The varnish offers a protective layer between the surface of the gut and the environment around it. This layer inhibits, but does not stop, the absorption of moisture, oil and acid into the string. The varnish layer is useful under a few conditions:
- If you perspire a lot
- If you live in a hot, humid environment, or it is summer time
- If you have an acidic touch
Under these conditions, the varnish can extend the life of a string. Moisture and acid break down the collagen bond that holds the fibers of the gut together and can cause fibers to separate and ultimately lead to the failure of the string.
This protection comes with a couple of trade-offs:
- The varnish makes the string a little stiffer
- The varnish can not be put on the string perfectly evenly, so the varnish creates a little inharmonic content to the string, particularly in the upper partial range. Those players with particularly sensitive ears may find that the varnished string sounds a little false.
The decision of whether to have your strings varnished or not is a personal one. For some players it will be a great help and to others it will make no difference.
Oiling Gut Strings
The question often arises as to whether or not gut strings should be oiled in an effort to preserve them and protect them from wear. In my experience, this depends very much on the individual needs of the musician.
You should consider oiling the strings if:
- You live in a humid climate
- You play in a humid environment like a small club
- You perspire a lot when you play
- You have rough skin that abrades the surface of the strings
Otherwise, it might not be necessary to oil strings.
If you do decide to oil your strings, we recommend a light nut oil such as almond oil. This is available in most grocery stores as it is used as a salad oil. It has a neutral pH, which is important for strings, as gut degrades when exposed to base and acid solutions. You will want to use the oil sparingly, and be sure to keep it off of the instrument varnish.
Musicians using a bow will need to be careful to keep the oil away from the area of the string that comes in contact with the bow, as the oil might coat the bow hair and cause it to slip on the strings.
Making Gut Strings
by Daniel Larson
For thousands of years, the choices of musical string materials were few. Usually it was limited to some indigenous material that was either suitable or adapted to the task. If you lived in the East the logical choice would be silk where the fibers were processed, twisted and braided into musical purity. Horse hair would be used if you lived in Scandinavia. In the more tropical regions plant fibers would be twisted and spun into a cord for use as a musical string. The European West chose an equally unlikely material for use as strings - animal intestines.
No one knows exactly when gut was first used for musical strings. Legend has it that Apollo was the first string maker. When he came across the tortoise and had the inspiration to make the first lyre he used the poor animal's own intestines for the strings. The first actual proof of the use of gut strings came in 1823 when Burton discovered some of the earliest extant musical instruments in the tombs of Thebes. These harps had gut strings that, according to his account, still made a tone after some two thousand years in storage(1).
So, gut has been the traditional material for strings in the West and still defines the standard of violin tone. The highest praise that can be lavished on one of the new, synthetic strings is that it sounds "as warm as a gut string". But what exactly is a gut string?
Gut strings are made from the small intestines of sheep. The process can be broken down into four basic steps:
1. Slaughter and recovery at the abattoir.
2. Dressing and selection.
3. String processing and twisting.
4. Drying and polishing
5. Wire winding. (Optional step).
Step one - The abattoir. It all begins at the abattoir. The intestine is also known as a casing and is referred to in the trade as a "set". The intestine must be pulled from the animal immediately after slaughter while the gut is still hot. This will insure that the blood vessels that run into the casing will be broken off close to the gut wall. To allow the organs to cool will risk having these veins break off as much as 1.5 inches away from the casing wall. This creates "whiskers" that lower the quality of the gut for musical string use. These whiskers are almost impossible to get rid of and will inhibit the quality of the string by introducing a contaminating agent in the muscular membrane. Whiskers also increase the likelihood of a false string because they change the otherwise regular linear mass of the gut. To insure the best quality the gut must be removed immediately, separated from the fat, stripped of manure and put into cold running water. The presence of fat will inhibit the bonding of the fibers during the drying process. Manure will cause stains in the set which are difficult to get rid of. The cold water will help preserve color and strength of the casing. Once a group of five or so sets are stripped they are bunched and knotted in the center. This is known as handling the casing "on the double", that is, at the center. Such an arrangement makes it easier to handle the thirty yards of length and eases the strain on the material. These bundles are put into large containers and await collection by the dresser.
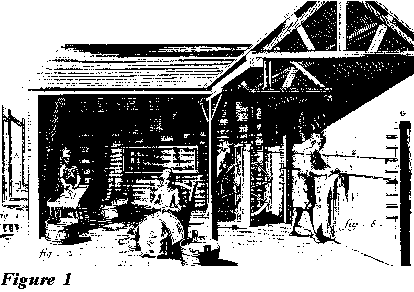
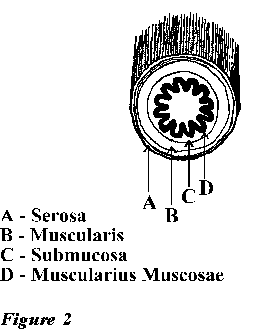
Step two - the dresser. Traditionally the string makers were located very close to the slaughterhouses. Denis Diderot in his Encycloédie of 1865 mentions this fact and gives an illustration and explanation of the process, (figure 1).(2)
No doubt this was important in the past when shipping and storage methods were limited. It was easier to bring the live animals into the city center where they could pe processed quickly with little spoilage. In earlier times the string maker would do most of the selection and dressing of the casings. Sometime, I believe in the
early 1900's, some spec ialization took place and the task of selection was given over to the dresser. Today modern methods and technology allow supply and production to be separated by greater distances. Plastic and stainless steel containers allow the material to be stored for long periods without change of color or deterioration. Along with advances in preservation, highway and air shipping methods allow the abattoir, dresser, and string maker to be located anyplace on the globe.
When the casings arrive at the dresser from the abattoir they are soaked in cold water. This soaking may be for a few hours , overnight, or several days depending on the methods of the dresser. Soaking softens the submucosa membrane and prepares the set for crushing, (figure 2). After the cold soak some dressers will provide a hot soak for an hour or so before machining.
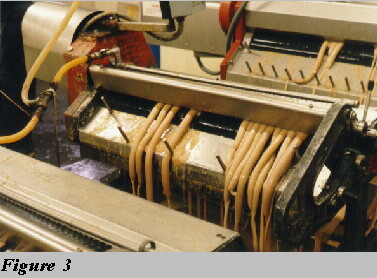
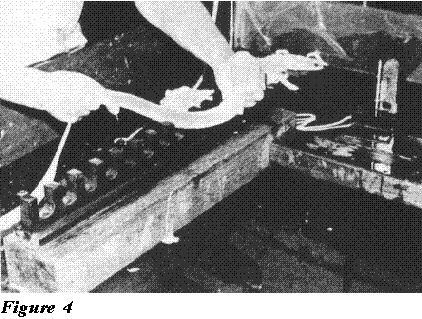
The next step is to remove all membranes except for the muscle fibers that will be used in making the strings. This is called stripping and crushing the casing. Traditionally stripping and crushing was done on wooden boards with a metal bladed scraper. This is hard work. The task is to strip off the outer serosa layer while at the same time crushing the inside mucosa membrane. When scrapped with enough vigor the mucosa will liquify and be squeezed down and out the casing tube. Fortunately, a machine has been developed to implement this task. It is known as the crusher/scraper, (figure 3). The sets are sent through the crusher/scraper doubled at the middle. They go through a set of three rollers. The first two sets crush the mucosa membrane and squeeze the gut tube to push the liquified membrane down through the casing. The third set of rollers is a specialized set called the dethreader/finisher which squeezes the last of the mucosa out of the tube and separates the outside serosa membrane from the muscle layers. Serosa is known in the trade as "thread" because it resembles a long white thread. The casing leaves the scraper plant as a clean tube of muscle fiber twenty five to thirty yards long. It is now ready for sorting.
Sorting takes place on the sorting table. This is a stainless steel or rubber surface about waist high that has one or two water spigots set into it. First, the casing is checked for length. Then one end of the tube is filled with water to inflate a section of the tube about eight to twelve inches long. This inflated section is used to gauge or caliber of the casing. The gauging system has four ranges that separates the casings by outside diameter, (table 1).
Gauge | Diameter |
Narrow | up to 18 mm |
Medium | 18 mm - 22 mm |
Wide | 20 mm - 24 mm |
Extra-Wide | 23 mm + |
Casing caliber is checked with a small rack that consists of six or seven slots of varying width, (figure 4). The first slot is 18 mm wide, the next is 20 mm, then 22 mm and 24 mm. The last two or three slots are not used for sheep but reserved for hog and beef casings. Workers will test the inflated tube in the various slots until the most comfortable caliber is established. Then the water in the filled section will be run down the length and the caliber checked again at several points. As the water is moved through the tube it is also checked for holes. Small pin holes are to be expected. These are where the blood vessels entered the tube. Slightly larger holes can be left in the length. Large holes mark spots where the casing is cut. At the same time the casing is being checked for color and general condition. Quality can vary with breed and age of animal, elapsed time since slaughter, weather conditions and handling. Great judgement is required to take all of these factors into consideration and select the best use for a casing. These dressers are skilled workers and lay the foundation for the quality of the gut string.
Intestines are not the same diameter along the entire length. The upper section is wider in diameter for about 20 yards than the lower section. This is referred to as the first cut, being the first part of the casing and the most valuable to the dresser. First cuts are usually 22 mm - 24 mm and are valuable for sausage casings. The lower section of the casing is known as the second cut and can measure from eight to fifteen yards. Second cuts are typically 18 mm - 20 mm. These are the best for strings. Not only are the first and second cuts different in size, but they also differ in structure. The function of the upper section is to constrict around and pulverize food in the digestive tract so the nutrients can be extracted so the muscle fibers are shorter and oriented more around the circumference of the tube. As the food is moved down the intestine the muscle fibers lengthen because the function is more to push the used material down. These longer fibers assist in making stronger, more stable strings. It is fortunate that the smaller size makes the casing less valuable so the cost of the string material can be kept as low as possible.
Selected casings are grouped together in hanks. Hanks consist of about 100 yards of material. Hanks are stored in salt that has been processed especially for use on casings. The salted hanks are stored in barrels in a semi-dry condition until the string maker is ready for them.
Step three - the string maker. The first task of the string maker is to re-hydrate the hanks of gut and wash the salt out. This is usually done with an alkaline solution of some kind. The 14th century Secretum philosophorum(3) recommends the use of lye. In the 18th century De la Lande(4) notes that the Italians used wine lees as an alkaline agent and the English, French, and Germans used potash. Today the custom is to use soda ash to create a base solution for the gut. The strength and temperature of the solution is critical(5). It is possible to reduce the gut to a gelatinous mass if the solution gets too strong or too warm.
As I have mentioned before, the gut comes to the string maker as a long tube. Traditionally there have been some string makers who specialized in what is called "whole gut"string making. That is, they made strings from the whole, round tube. To understand the implications of this I would like to consider the configuration of the intestine. It is tubular in shape, but it is not a straight tube. In the body the intestine curves back and forth so that a long length can be packed economically into a small space. One side of the intestine, the outside of the curve, is longer than the inside. So, when you stretch out a whole gut, the inside will become tight with the longer outside section dangling from it. This means that there are many of the muscle fibers that are not distributing the tension of being pulled. To twist a number of these whole guts together is to have a string that does not distribute the tension evenly between the muscle fibers. To solve this problem the Germans, according to De la Lande, developed a device called the splitting horn, (figure 5). This is also known as a soutil or subtle, taken from the Italian word sottile which means narrow or slender.(6)
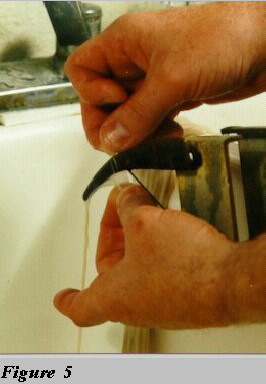
This tool w ill divide the gut length into two or more ribbons. The ribbons can then be stretched more straight and spread the tension of the string more evenly through the muscle fiber structure. The splitting horn is a wonderful tool.(7) The traditional sheep gut horn consists of a curved mandrel with a blade that crosses the plane at 90º. The gut tube is drawn over the end of the mandrel, and is split on both sides by the blade. The curve of the mandrel is more or less the same curve as the gut tube so the casing always remains in the same orientation to the blade. The yield is two ribbons of different widths. The widths can be controlled by moving the blade back and forth along the horn as the slot cut for it is long enough for this purpose. The gut is pulled over the horn and across the blade. When the arms are extended fully the ribbons are dropped and the hands moved forward to grab the blade for another pull. This action is repeated until the gut is fully split.
The two ribbons are referred to as "rights", or "smooth side", and "lefts", or "rough side". Both ribbons have special uses in string making because of their individual qualities. The rights are cut from the outside of the casing where the fibers are a little more pure. When the ribbon is laid flat the edges are smooth and straight. The rights are used for the treble strings up to a diameter of one millimeter or so. However, I do use rights for the cello a-1 string which goes to a diameter of 1.28 mm but this is a special use. Lefts are made up of the inside of the casing. The villi and other blood vessels are located at this point on the gut. When the lefts are laid flat the edges are rough and irregular. Lefts are used for larger strings where strength is not so crucial but a build up of mass is necessary. I use them for the cello d-2, (1.50 mm), and larger diameters of strings.
After a batch of gut is split it is ready for cutting and processing. I usually run batches of three hanks at a time. There can be any number of batches in process at any one time, but I find the three hank batch a manageable amount. I have two lengths of twisting rack in the shop. One twists a string length of eighty four inches and the other a length of fifty five inches. This way I am twisting two or more violin strings or one or more cello strings at a time. Ribbons will be allocated to one rack or the other depending on length. Shorter lengths are discarded. I have decided that anything shorter is not worth the time to fuss with.
The processing is basically a controlled fermentation of the gut. Enzymes in the gut are activated by the alkaline solution and heat. Careful monitoring of the solutions and frequent changing of the water cause the oils and fat to break down in the gut leaving a pure fibrous collagen structure. Solutions are changed four times a day and the gut will be scraped at least once a day. This aids the removal of extraneous matter that may be stubbornly adhering to the gut. I use a black plastic board as a base to scrape on. The wet gut becomes translucent over the black background and it becomes easy to see flaws and imperfections in the material. This process goes on for four days. If done correctly the gut comes out as long, beautiful white ribbons. If the solution is too warm or too strong the gut will break down and become useless.
The next step is to whiten the gut in some way. If the gut is brought straight from the processing solutions to the twisting bench the strings will come out some shade of yellow-brown. The particular shade will depend on the quality of the material, handling, minerals in the water, etc. The tradition has developed to whiten and clarify the gut. There are two primary ways this is done. One is with sulphur fumes and the other is with a bleaching solution.
In the fuming process the strings are first twisted on racks and the racks of strings are gathered in a small room that can be tightly sealed. The strings are still slightly damp and freshly twisted. When the room capacity is reached, a quantity of sulphur powder will be placed in the room and set on fire. The room will then be tightly sealed to prevent the infiltration of air. In the sealed room the sulphur will consume the oxygen and create new sulphur dioxide compounds in the air that will act on the gut strings. The effect is to whiten the gut. When the strings are taken out of the sulphur room they are sometimes re-twisted and fumed again, depending on the techniques of the maker.
The other method of whitening is to put the gut in a bleaching solution. The usual agent is hydrogen peroxide. The peroxide is mixed into a water solution and the gut is immersed for a period of three or four hours. Care is taken to keep the gut down in the water as hydrogen bubbles form on the gut and cause it to float. I use two bleaching cycles since I prefer a gentle soaking over a longer period of time. The gut is allowed to rest overnight before it is twisted.
The twisting bench consists of a long table with a head stock of spindles at one end and a bank of hooks at the other called the "lazy end". Exact configurations will vary greatly with each manufacturer but the principle remains the same. Gut ribbons are bundles together and twisted between a spindle at one end and a hook at the other.
The ultimate diameter of the dry string depends on the width of the gut ribbon and the number of ribbons that are twisted together. More ribbons creates more mass and therefore a thicker string. A chart of average string bundles is given in table 2.
String | Ribbons | Side |
Violin e-1 |
3 | Right |
Violin a-2 | 8 | Right |
Violin d-3 | 15 | Right |
Viola a-1 | 8 | Right |
Viola d-2 | 15 | Right |
Cello a-1 |
24 | Right |
Cello d-2 |
15 | Left |
Bass G-1 |
21 | Left |
Bass D-2 |
38 | Left |
Bass A-3 |
64 | Left |
The ribbons are counted out and tied to a string loop that is hooked onto the spindle. The string bundle is then combed through with the fingers to straighten the ribbons and distribute the tension evenly between them. Then the bundle is tied to another string loop at the other end on the lazy hook. The ribbons are not pulled tight, but rather sag in the middle. This is referred to as the "swing". Thicker strings require more swing than thinner strings to develop the necessary angle of twist. Ratios of swing to string length to diameter to twist angle are proprietary to each shop and greatly influence the quality of the finished string. Generally speaking, twisted fibers reach maximum strength at a twist angle of about 17º. The strength of the twisted structure will decrease somewhat as the angle increases, but the flexibility of the string will increase.(8) This is the essence of the art of string making. The playing characteristics of the string depend on the kind of gut and how it was processed and twisted.
Once the gut has been twisted it must be dried and seasoned. The drying process must be very slow for the collagen in the gut fibers to bond together properly. Twisting should be done in a very damp environment. As the string is twisted, water is wrung out of the fibers. The balance of the moisture is absorbed in the air around the string. When the string losses this moisture it also losses diameter and begins to shrink down upon the center of the twisted structure. As the string shrinks in diameter it gains in length and the string becomes slack between the two hooks. It is therefore necessary to add more twist to the string to tighten it again. Usually the string is wetted and tightened in this manner numerous times a day over two or three days before it settles down and becomes stable. The string is then allowed to dry and season for two to four weeks before it can be polished.
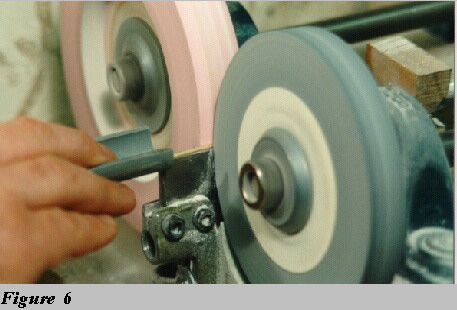
String polishing has had various meanings through the history of string making. Traditionally this was done just after the string was dry and before it was taken off of the string rack.(9) The usual method was to rub the strings with horse hair pads that were treated with oil and pumice powder. These pads were rubbed back and forth along the strings to remove imperfections and smooth the string up a bit. This method did nothing to true the string or make the diameter regular. Consequently history rings with complaints about strings being false and irregular. Motzart and Sphor both comment that strings are smaller at one end than at the other and there are elaborate methods of dealing with this problem.(10) This problem originates with the way strings are twisted. Since the gut is twisted from one end, the twist must build up at that end before it is transferred to the other end. This causes one end to twist more tightly at one end than the other, causing that end to be slightly thinner due to the extra twist. This problem persisted until someone, probably the Pirazzi family in the mid 1800's(11), came up with a way to make the string a regular diameter throughout the length. At this point the concept of polishing becomes one of rectifying the cylinder of the string to make it round and uniform. This was first performed, I believe, with a mechanism known as a flat bed polisher.(12) This polisher consists of a long table with hooked spindles at each end. The spindles are connected from end to end so that they turn at the same rate. Strings can be mounted on the hooks and rotated as on a lathe. With the strings spinning two boards lined with sandpaper were moved back and forth along the bed. By regulating the space between the boards the strings would be sanded to a regular cylinder. While this machine was an improvement it did not work perfectly and a lot of strings were still false. The concept of the centerless grinder was introduced to the string making world sometime in the mid 20th century and revolutionized the trade. With the introduction of this machine the string maker could almost guarantee that each string would be perfect in fifths. The mechanism consists of two abrasive wheels turning in opposite directions with a space between them, (figure 6). One wheel is set at an angle and acts as a drive wheel that pulls the string through at a regular rate. The other wheel is an abrasive stone that removes material from the string. By regulating the space between the wheels the diameter of the string can be controlled to perfection. The freshly twisted, unpolished string is usually reduced by 20% to form a regular cylinder. Removing too much of the string diameter will result in a compromise of the twisted struct.
Strings are twisted in many different sizes so that a string can be polished to a specific diameter without exceeding a reasonable tolerance. Some string makers use a liquid lubricant on the string as it goes through the polisher which serves to flush away string dust and provides a finish. This fluid has a low flash point and can be a bit of a fire hazzard so I prefer to polish the strings dry and finish them by rubbing with the traditional oil, pumice, and cloth.
I know that the use of gut strings will be greatly specialized in the future. Many modern materials have been developed that do more or less the same job with fewer problems. However, I feel that is important that violin makers, repairers and players have some understanding of the art of gut string making. Synthetic strings will always be compared to gut. This will serve as our bench mark because there is no sound more beautiful than the tone of a good gut string.
1. J. G. Wilkinson "The manners and Customs of the Ancient Egyptians" Vol. I 1878
2. This illustration and partial translation of the text can be found in the catalog "Shapes of the Baroque: The Historical Development of Bowed String Instruments". Presented by William L. Monical under the auspices of The American Federation of Violin and bow Makers, Inc. Copyright 1989 by The American Federation of Violin and bow Makers, Inc. Library of Congress Catalog Card Number: 89-83602.
3. Werner Bachman, "The origins of Bowing" Oxford University Press 1969, p.81
4. De la Lande wrote about the string making process in Italy in the late 18th century. A synopsis of his comments can be found in "The Violin: Its History & Construction" by Able and Niederheitmann, translated from German by John Broadhouse. 1st edition 1864 2nd eddition 1874. Published by William Reeves.
5. De la Lande partually attributed the high quality of Italian gut strings to the warm climate in which they were made. He specified that the best time was from Easter to October. Able and Niederheitmann, p 84.
6. Alberto Bachmann "An Encyclopedia of the Violin" Da Cappo Press, New York 1966
7. When I started trying to make gut strings I had read about this device but I had never seen one. I tried to make a "splitting horn" with one miserable failure after another. One day I was discussing my problem with Glenn Bjorkman of the Victor Companies. He kindly sent me two old splitting horns that his company used for sheep gut. When I saw them I knew at once what I had been doing wrong and have forever been impressed with this simple, elegant and functional tool.
8. For a detailed study of the principles of twisting I would recommend "The Technology of Cordage Fibers and Rope" by David Himmelfarb, 1957. Textile Publishers, Inc.
9. "Violin Making as it was, and is" by Ed. Heron Allen, p. 212
10. "Sphor's Violin School" edited by John Bishop. Robert Cocks & Co. London. I am not sure of the date of this publication but the original "Violin School" was published in 1831.
11. This is only speculation on my part. I have not had the opportunity to research the issue thoroughly. The contributions of the Pirazzi family to the history of string making have been considerable.
12. This machine has been described to me by Glenn Bjorkman of the Victor Companies.
I am grateful to Glenn Bjorkman and Frank Smith for their patience and assistance through the years as I learned about the process of making gut strings.
LOADED GUT BASS STRINGS "C" TYPE
"There is another sort of strings, which they call Pistoy basses, which I conceive are none other than thick Venice-Catlins, which are commonly dyed, with a deep dark red colour." (Thomas Mace 'Musick's Monument', London 1676)
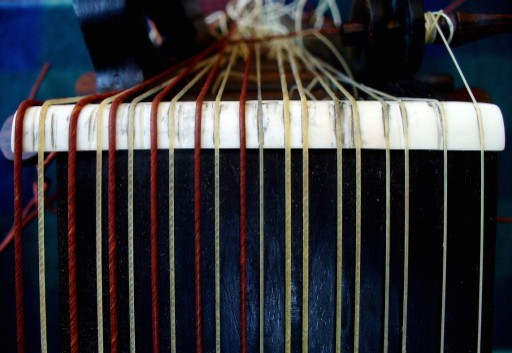
11 course d minor lute set-up
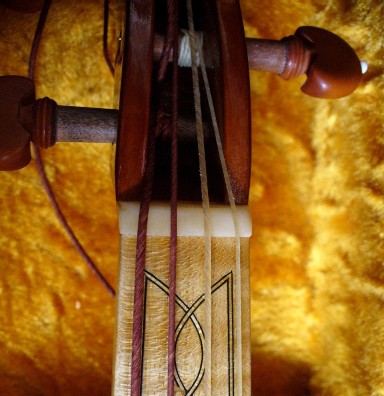
Viola da braccio set-up (the 11th bass loaded string is of 1.30 mm diameter = 2.00 equivalent gut)
INTRODUCTION
The appearing of wound strings caused, starting from the end of the 17th century, the definitive abandoning of the ancient manufacturing techniques of the traditional all-gut bass strings. This explains why modern plain gut strings fail to produce an acceptable acoustical performance in the low registers, thus making it unavoidable to use wound strings for musical repertoires that actually pre-date their historical appearing; this, in turn, causes an obvious philological paradox as well as serious tone and balance problems between high and low registers. A large number of bass stringhole diameters recorded from original Lute bridges dating from the late 16th and 17th century shows that those holes are too small to allow plain gut strings a sufficient working tension at the proper pitch. Musical iconography from the 17th century also shows often bass gut strings of quite different colors from that typical of plain gut, varying from dark red to brown only. Treatises of the time confirm, too, that strings possessed a remarkable duration of sound and acoustical exuberance (see: Mersenne 'Harmonie Universelle', Paris 1636; 'The Mary Burwell Lute Tutor', 1670 ca.).
All this suggests a rivolutionary hypothesis: the loading of gut, a technological strategy that we believe employed by the ancient string-makers in order to render the strings to be used in the low registers more sonorous.
Iconographical examples
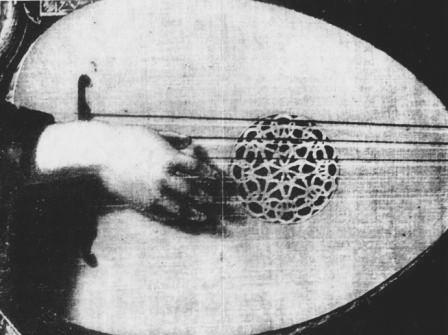
7course lute: detail
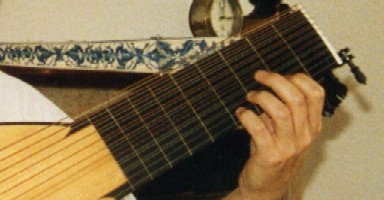
F. Le Troy (1690 ca.) Detail of the Charles Mouton's portrai
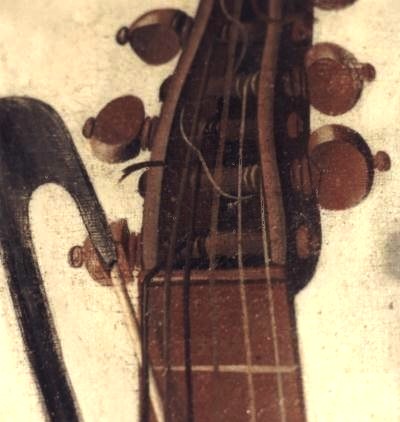
Jakob Lindberg playing his 11 course d- minor lute
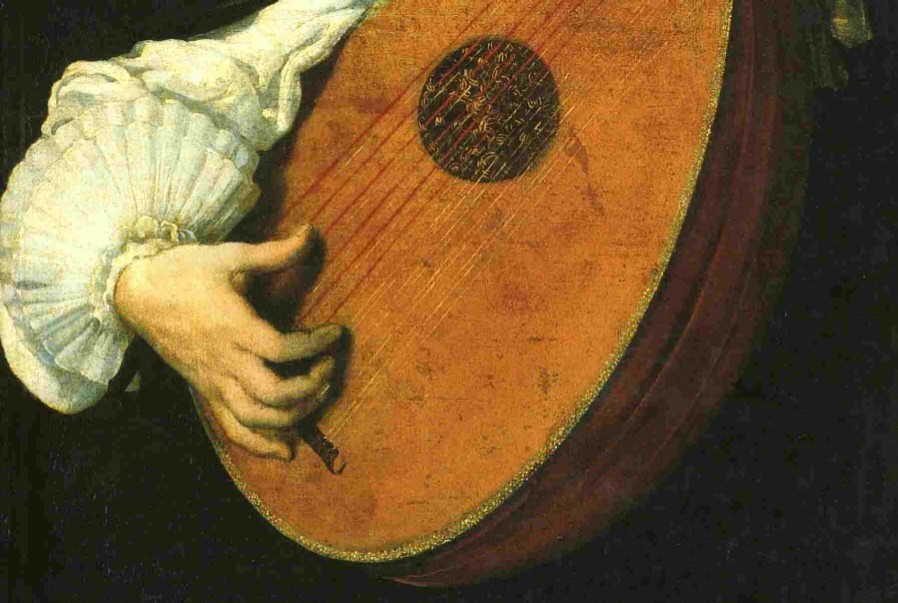
Anonymous dutch painter, 1st half of the 17th C: detail
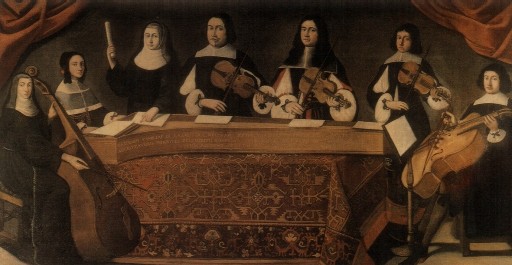
Anonymous french painter, 1st half of the 17th C: detail of the lute player
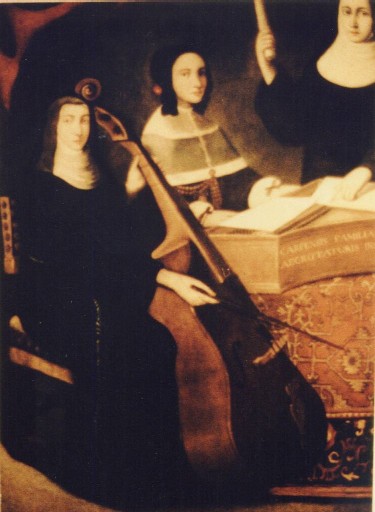
Girolamo Martinelli, 2nd half of the 17th C: Concerto in casa Lazzari
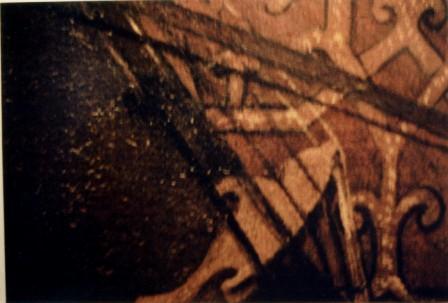
Girolamo Martinelli: detail of violone
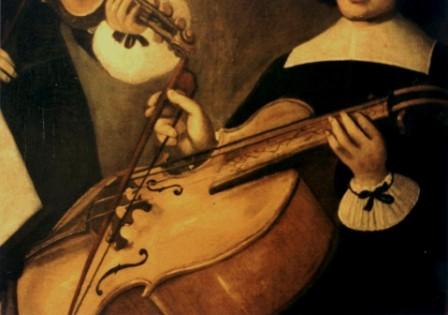
Girolamo Martinelli: detail of the violone strings
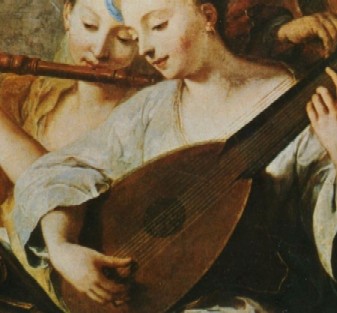
Girolamo Martinelli: detail on the bass-violin string
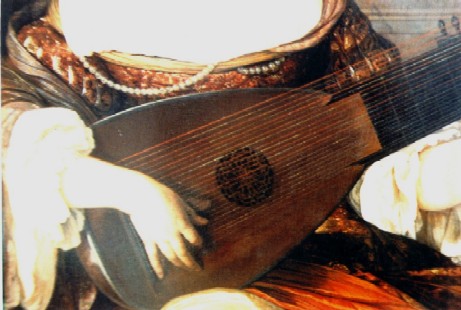
Francois le Troy, 2nd half of the 17th C: detail on the brown basses
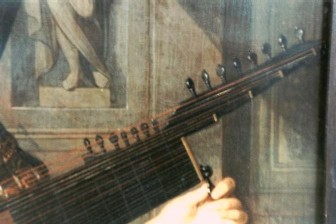
Anonymous dutch painter, 2nd half of the 17th C: detail of the red bass strings on a 12 course lute Rutilio Manetti, Siena 1624: detail on the brown Lute bass strings and on the Violin brown 3rd & 4th strings ("...best strings are Roman 1st & 2nd of Venice catlins: 3rd & 4th best be finest & smoothest Lyons, all 4 differ in size..." James Talbot's manuscript, 1695 ca)
Completely re-designed!
Special smooth roped gut strings (like ours VENICES ) characterized by a high, standardized specific weight (twice than natural gut) , achieved by a loading process with metallic copper powder. Diameters smaller than 180 C are manufactured with a gradual loading decrease, in order to keep the otherwise excessive brightness of sound of the thinner strings under control and at the same time to obtain a higher tensile resistance and a longer playing life.
Reddish brown color,oiled surface.
ACOUSTICAL PROPERTIES AND FIELD OF APPLICATION
Strong and warm tone, without the excessive brightness typical of wound strings, perfectly coherent with the tone and dynamics character of gut high strings. Excellent in staying in tune, better than any plain Gut, Nylon Nylgut and wound strings available today.
Indispensable for Renaissance and Baroque stringing till the 1st half of the 17th Century, in the strictest respect to authenticity.
WHAT MEAN 140 C ?
To keep calculations simple and make it possible to use any available string-calculator, C type loaded gut strings, as well as wound Nylgut ones D and DE types, are referred to by a letter following a number indicating the theoretical equivalent diameter of a plain gut string.
E. g. "140 C" stands for a loaded string (indicated by the letter "C" ) corresponding to a high twist gut of 1.40 mm. in diameter. The actual diameter of the strings is, of course, smaller but under playing conditions it will have the same working tension as a gut string of 140 mm. diameter at equal pitch.
Notice! These strings are made for basses only. Please do not use them as cello 2nd & 3rd (cello must work with wound strings), Gambas 3rd & 4th; Viola da braccio 2nd.
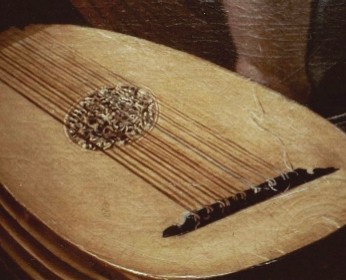
measurement made on the Charles IX Andrea Amati's viol (1570 ca).
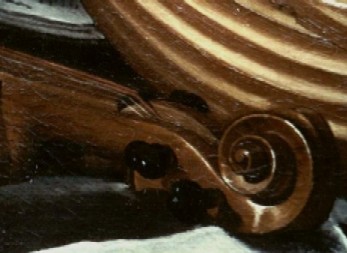
Ashmolean Museum, Oxford maximum passing diameter: 2.30 mm
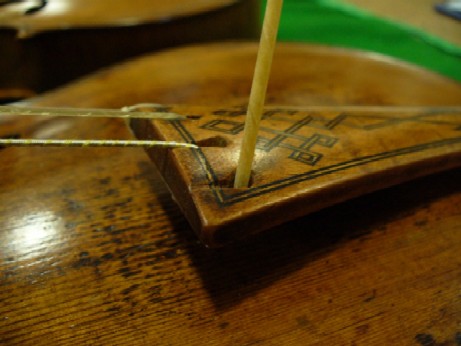
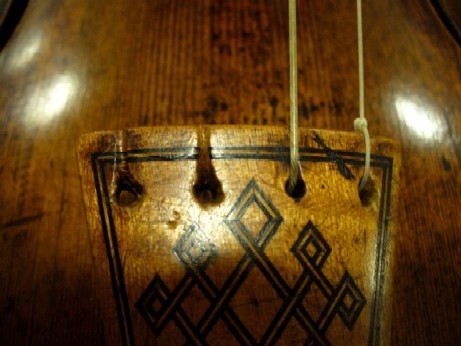